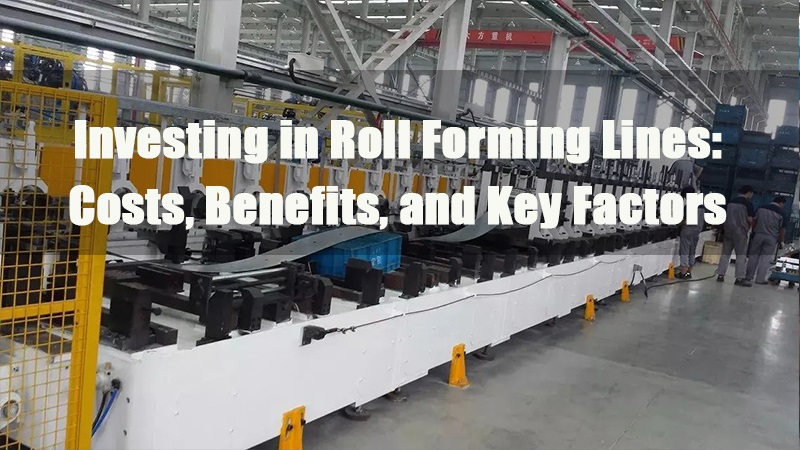
辊压成型已成为钣金制造和型材制造中的关键工艺,因其高效、高精度和先进的自动化能力而备受业界关注。对于希望提高生产力、降低成本或拓展产品多样性的制造商而言,投资辊压成型生产线是迈向长期增长的关键一步。
然而,要确定这项技术是否合适,需要根据生产目标、预算限制和设备性能进行全面评估。本文深入探讨了四种基本类型的辊压成型机,概述了标准生产线和自动化生产线的技术特点,并重点介绍了设备成本、生产效率、系统集成和运营维护等核心投资因素,帮助您做出明智的决策,最大限度地提高投资回报。
1.0四种基本类型的辊压成型生产线
1.1辊压成型术语表
学期 | 定义 |
死 | 压力机内部用于冲孔或切割的工具。可能包括冲头、刀片、剪床、锯子或封口模具。 |
飞骰子 | 在材料移动的同时进行冲压操作的模具。模具随材料一起移动,也称为“不停歇”。 |
停止 | 材料暂停以进行压机操作。也称为“停机切割”或“停机/启动”。 |
闭环 | 伺服系统用于控制位置或速度。模具或材料的移动精确同步。 |
开环 | 无伺服反馈。控制基于安装在物料上的编码器。 |
促进 | 在开环飞模装置中,气动缸或液压缸有助于使模具速度与材料流动相匹配。 |
踢球者 | 利用压力机运动推动模具向前的机械增压——直接与压力机行程相关。 |
模具加速器 | 用于闭环飞模系统;指使模具与材料速度同步的伺服驱动系统。 |
执行器 | 将伺服系统连接到模具的机械部件(滚珠丝杠、皮带和滑轮、齿条和小齿轮)。 |
辊压成型机 一般属于 四个基本类别,由两个关键参数定义:切割过程中材料是否停止,以及系统是否采用闭环伺服控制。这些类型包括:
- 开环停止
- 开环飞模
- 闭环停止
- 闭环飞模
其他自定义或混合配置通常基于这四种配置的变体或组合。了解这些类型对于驾驭更复杂的系统架构至关重要。
分类依据:
辊压成型生产线按以下标准分类:
- 控制系统:是否采用闭环伺服系统进行精确定位和反馈。
- 操作模式:压力机操作过程中材料是否停止或继续移动(飞模操作)。
1.2开环停止
- 控制:开环
- 手术:材料停止切割或冲孔
- 成本: 低的
- 准确性: 缓和
- 输出: 低的
该配置使用开环控制来定位材料,并在每个压制周期之前停止。
工艺变体:
- 后期剪辑:先将材料滚压成型,然后使用固定模具切割。适用于大多数标准应用。
- 预切:材料在进入成型段之前被切割成所需长度。这种配置的产量较低,但工具成本较低,非常适合预算有限的企业。
1.3开环飞模
- 控制:开环
- 手术:在材料运动时进行切割
- 成本: 低的
- 准确性:中等(±0.032 英寸/0.81 毫米)
- 输出: 高的
飞模系统随着材料的移动进行切割,模具的移动速度与材料的速度相匹配。
附加说明:
模具通常通过弹簧或气缸返回。
如果材料强度不足以支撑模具质量,则 增压缸 可以添加以辅助加速并减少阻力负荷。
1.4闭环停止
- 控制:闭环伺服
- 手术:材料停止切割
- 成本:中到高
- 准确性:高(±0.003 英寸/0.076 毫米)
- 输出: 缓和
该系统使用伺服反馈来控制材料定位并提高切割或冲压操作的重复性。
技术说明:
通常使用伺服驱动的进料辊。
如果出现进料滑落问题, 材料编码器 可以添加以提高反馈准确性并确保精度。
1.5闭环飞模
- 控制:闭环伺服
- 手术:在材料运动时进行切割
- 成本:最高
- 准确性:极高(±0.015 英寸/0.38 毫米,最高可达±0.0002 英寸/0.005 毫米)
- 输出:最高(高达 600 fpm / 183 mpm)
这是最先进的配置,能够使用伺服同步飞模系统实现高速、高精度成型和切割。
系统设计:
模具由 滚珠丝杠执行器.
精准 伺服电机 通过花键联轴器与模具机械耦合,以确保精确同步。
控制系统不断调整模具运动以实时匹配材料速度和位置。
1.6汇总比较表
类型 | 控制系统 | 切削条件 | 精度(英寸) | 成本 | 最适合 |
开环停止 | 开环 | 已停止 | 中等(~±0.03) | 低的 | 标准化、成本敏感的生产 |
开环飞行 | 开环 | 连续的 | 中等(±0.03) | 低的 | 中速连续运转 |
闭环停止 | 闭环伺服 | 已停止 | 高(±0.003) | 中至高 | 精密冲压或切割 |
闭环飞行 | 闭环伺服 | 连续的 | 非常高(±0.0002) | 最高 | 高速、高精度输出 |
2.0标准辊压成型生产线
辊压成型技术以其高效、精准和高度自动化,已成为现代金属板材和型材制造的基石。标准辊压成型生产线配备灵活的设计和先进的控制系统,能够满足各种行业需求。
2.1主要特点:
现代辊压成型机通常具有以下核心优势:
- 技术可靠性:专为长期连续运行而设计,停机时间最短,确保稳定生产。
- 高灵活性:快速简便的工具更换可以快速适应不同的形状和轮廓尺寸。
- 支持柔性制造:集成先进的软件和编程,实现高效、无浪费的操作。
- 多功能处理:可在一条生产线上完成预冲孔、开槽、后冲孔、弯曲、滚压成型和快速切断。
阿莱克夫斯 专注于高性能辊压成型生产线的设计和制造,结合丰富的行业经验,并高度重视设备的可靠性、安全性和灵活性。所有系统均支持快速换模,并适应各种型材尺寸,使其成为钣金加工领域各种工业应用的理想选择。
3.0全自动辊压成型生产线
全自动辊压成型生产线专为高效、大规模金属型材生产而设计。这些系统集成了 开卷机、自动缝焊机、辊压成型机和智能堆叠单元——提供从原始卷材到成品堆叠的完整端到端自动化解决方案。
该生产线采用多条辊压成型通道,并采用模块化配置,用于校平、校直、成型和切割。翻转和堆叠系统配备夹持爪、伺服导轨、真空机械臂和智能定位模块,确保高效、安全、有序地处理产品。
3.1技术优势:
- 全流程自动化:自动线圈装载和焊接, 连续进料、在线切割和堆叠——无需人工干预。
- 多级精密成型:滚轮站采用渐进变形段设计,以实现高精度的复杂轮廓几何形状。
- 自适应对准系统:左右对准和垂直偏移滚轮确保整个生产线上线圈跟踪准确、稳定。
- 模块化伺服控制平台:独立的伺服控制滑动平台可实现精确的机器人处理和堆叠操作。
- 高度灵活性和可扩展性:支持多种材质、厚度、型材截面,可根据具体生产需求配置设备参数。
该系统非常适合大规模生产 C 型槽、U 型槽、电缆桥架、太阳能电池板支架、门轨、轻钢框架等,使其成为现代金属加工智能自动化的关键推动因素。
4.0投资辊压成型生产线时要考虑的关键因素
辊压成型线是钣金加工和型材制造中必不可少的设备。为了确保投资合理,必须评估几个关键因素,以平衡资本成本和长期生产效率。
4.1机器成本和使用寿命:
- 初始投资:标准辊压成型生产线(包括开卷机、切断系统和控制电子设备)通常包括 $100,000 至 $500,000,很大程度上取决于成形机架的数量和尺寸。中型系统通常介于 $150,000 和 $250,000.
- 耐用性:这些系统经过精心设计,使用寿命长,没有实际使用寿命限制。如果维护得当且不误用,它们会表现出 极低的故障率 和 最低的更换零件成本.
- 设计稳定性:虽然在精度、易用性和耐磨性方面不断改进,但核心机械结构仍然保持不变 稳定可靠 随着时间的推移。
4.2生产吞吐量和转换成本:
- 标准速度: 大多数辊压成型生产线的运行速度为 100 英尺每分钟 (fpm)或粗略地 每分钟30米,可根据生产需要调节速度。
- 典型日产量:考虑到装载、穿线、清洁和其他停机时间,平均每日产量达到 25,000 至 30,000 英尺(7,600 至 9,100 米)在一个 8小时轮班.
- 转换效率:虽然转换成本随公司规模、产品种类和工作复杂性而变化,但辊压成型被广泛认为是 转化率低 成本 和 生产效率高 与其他金属成型工艺相比。
- 控制系统优化:现代电气和计算机控制大大提高了生产转型的灵活性和响应能力。
4.3生产计划和系统集成:
当前技术允许滚压成型线与 ERP(企业资源计划) 或者 MRP(制造资源计划) 系统实现订单驱动、自动化调度。
典型的集成包括:
- 直接导入生产参数(长度、数量、孔型)来自订单系统
- 自动控制系统调整 尽量减少人工干预
- 型材贴标或喷墨标记 便于追踪和识别
- 实时生产数据反馈 用于质量控制和性能监控
此类集成可以通过 改造现有系统 或设计成 新安装,前提是该设施配备了支持实时数据通信所需的硬件和软件基础设施。
4.4操作、维护和培训:
除了硬件之外,长期稳定性和性能还取决于:
- 定期预防性维护 延长使用寿命
- 备件库存计划 尽量减少停机时间
- 为操作员提供专业培训确保安全高效使用
- 标准化生产管理 提高整体运营效率
参考
www.amscontrols.com/kb/roll-forming-the-four-basic-machine-types/