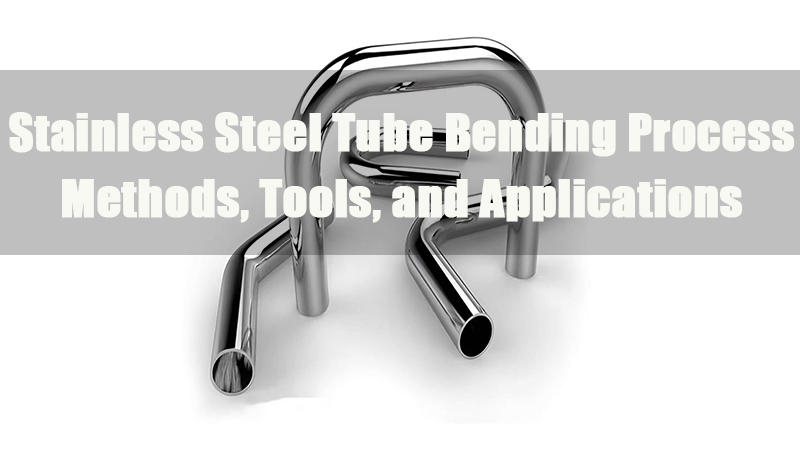
1.0Introduction to Stainless Steel Tube Bending Process
1.1Stainless Steel Material Characteristics and Bending Adaptability
Stainless steel is a critical material in industrial manufacturing due to its high strength, corrosion resistance, and excellent ductility.
Hard yet formable: With proper processes, stainless steel can be bent into complex shapes, making it suitable for customized prototypes and precision components.
Industry advantages:
- Durability: Corrosion and oxidation resistance make it ideal for harsh environments.
- Elasticity and strength: Provides both structural stability and forming flexibility.
1.2 Key Industry Applications of Stainless Steel Tube Bending
Industry | Typical Applications | Process Requirements |
Automotive | Exhaust pipes, chassis frames, fuel lines | High-precision bending, springback control, high-temperature resistance |
Medical | Surgical instrument brackets, medical tubing | Sterile surface finish, small-radius precision bending |
Construction | Handrails, decorative structures, curtain wall supports | High aesthetic demand, mark-free bending |
Energy | Oil pipelines, nuclear power components | Thick-wall tube bending, stress corrosion resistance |
2.0Challenges and Solutions in Stainless Steel Tube Bending
2.1Material Characteristics and Bending Difficulties
- High Strength and Ductility:Stainless steel combines high strength with good ductility, suitable for structural parts and industrial equipment.
- Challenges:High strength → requires greater bending force, increasing machine load. High ductility → prone to springback, affecting forming precision
- Corrosion Resistance:Surface damage during bending (e.g., scratches, dents) may reduce corrosion resistance, so excessive friction must be avoided.
2.2Processing Differences Among Stainless Steel Grades
Stainless Steel Type | Processing Features | Bending Challenges | Suggested Solutions |
304 Stainless Steel | Good ductility, widely used | Significant springback, radius control needed | – Springback-compensated die design – Over-bend slightly (+2°~5°) |
316 Stainless Steel | Molybdenum-added, stronger corrosion resistance but harder | Requires more force, prone to work hardening | – Use high-tonnage hydraulic/CNC tube bender – Reduce bending speed |
Duplex Stainless Steel | High strength, good toughness but difficult to process | Prone to cracking, complex springback control | – Preheat (200~300°C) – Use progressive multi-pass bending |
3.0Bending Process Methods Overview
Stainless steel tube bending can be achieved through various methods, each suited to specific pipe sizes, material properties, and precision requirements. Choosing the right process directly impacts forming accuracy, surface finish, and structural reliability.
This section introduces five common bending techniques—manual, hydraulic, CNC, roll bending, and hot bending—highlighting their suitable applications, equipment types, and standard operating steps.
3.1Manual Pipe Bending (Manual Pipe Bender)
Applicable Scenarios:Small batches, small-diameter pipes (generally ≤25mm), low precision requirements.
Equipment:Manual pipe bender (with dies of different sizes).
Operating Steps:
- Select the Die:Choose a suitable bending die based on the pipe’s outer diameter (OD).
- Fix the Pipe:Insert the pipe into the bender, making sure one end is against the positioning block and the bending start point aligns with the die center.
- Mark the Bending Position:Use a marker to indicate where the bend should start.
- Manual Operation:Slowly pull the handle to bend the pipe around the die to the desired angle (refer to angle scale).
- Springback Compensation:Since stainless steel is elastic, slightly overbend (by 2°–5°) to offset springback.
- Remove the Pipe:Release the clamp and check the bend angle and roundness.
3.2Hydraulic Pipe Bending (Hydraulic Pipe Bending Machine)
Applicable Scenarios:Medium to large pipes (DN15–DN150), medium to high precision requirements.
Equipment:Hydraulic pipe bending machine (with hydraulic pump, dies, clamping device).
Operating Steps:
- Install Dies:Install matching bending die, clamping die, and pressure die according to the pipe diameter.
- Set Parameters:Set bending angle (e.g., 90°) and speed (slower speed helps avoid wrinkling).
- Fix the Pipe:Place the pipe in the machine and secure it with the clamping die, ensuring the pipe end is aligned with the bending die.
- Start Hydraulic Pump:Press the button to activate the hydraulic cylinder, which rotates the bending die around its axis to bend the pipe.
- Hold Pressure:Hold the pressure for 2–3 seconds to reduce springback.
- Reset and Remove Pipe:Release the hydraulic system, remove the pipe, and check for dents or oval deformation.
3.3CNC Pipe Bending (CNC Pipe Bending Machine)
Applicable Scenarios:Complex 3D bends, large-volume production, high precision (e.g., automotive exhaust systems).
Equipment:CNC pipe bending machine (servo motor driven with PLC control system).
Operating Steps:
- Programming: Input bending parameters (angle, radius, feed speed) via the control panel or import CAD drawings.
- Clamp the Pipe: Feed the pipe into the loading rack; the machine will automatically clamp and align it.
- Automatic Bending:
- The clamping die holds the pipe in place, while the bending die rotates according to the program.
- A mandrel prevents pipe collapse and a booster prevents wrinkling.
- After each bend, the feeding unit moves the pipe to the next bending point.
- Real-time Monitoring: Laser sensors monitor actual bending angles and automatically compensate for springback.
- Product Output: After bending, the pipe is automatically discharged for quality inspection (e.g., pass-through gauge test).
3.4Roll Bending
3-Roller Bending Machine
Structural Features: Three-Roller Layout: One upper roller (active pressing roller) + two lower rollers (fixed supporting rollers).
Adjustment Method: The upper roller moves vertically; lower rollers have fixed or adjustable spacing.
Applicable Scenarios:
- Pipe Types: Stainless steel round pipe, square tube, flat steel, etc. (moderate wall thickness).
- Bending Radius: Suitable for large-radius arcs (e.g., guardrails, handrails, circular structures).
Operating Steps:
- Adjust Upper Roller Pressure: Set downward pressure of the upper roller based on pipe diameter and wall thickness.
- Feed and Align Pipe: Feed the pipe between the three rollers, ensuring the start end aligns with the rollers.
- Initial Pre-bend:
- Start the machine; upper roller presses down and the pipe rolls to form an initial curve.
- If pipe ends are not bent (due to straight-edge effect), pre-bend ends with die if necessary.
- Progressive Bending:
- Repeat rolling passes while gradually adjusting the upper roller pressure until the target arc is achieved.
- Check Roundness: Use an arc template or laser measuring device to verify bending consistency.
5-Roller Bending Machine
Five-Roller Layout: Two fixed lower rollers (support) + two side rollers (guiding) + one upper roller (active pressing).
Advantages: More stable than 3-roller design; suitable for high-precision, complex arc bending.
Applicable Scenarios:
- High Precision Needs: Such as automotive exhaust pipes, aircraft conduits, precision mechanical parts.
- Thin-Walled Pipe Wrinkle Prevention: Side rollers reduce deformation and prevent indentations.
Operating Steps:
- Adjust Roller Spacing:
- Set positions of lower and side rollers according to pipe diameter to ensure central alignment.
- Pre-bend Ends (Optional):
- If pipe ends need to be bent, use dies or hydraulic press for pre-bending.
- Feed and Align Pipe:
- Insert the pipe into the 5-roller system, ensuring even contact with all rollers.
- Progressive Rolling:
- Upper roller presses down, side rollers guide, and the pipe is formed through repeated rolling.
- Dynamic Adjustment:
- Monitor bending radius in real time; fine-tune side roller pressure to control springback.
- Final Inspection: Check roundness, arc smoothness, and dimensional tolerance.
7-Roller Bending Machine
Seven-Roller Layout:
Three lower rollers (main support) + two side rollers (guiding) + two upper rollers (pressing).
Advantages: Ideal for extra-large diameters (>300mm) or thick-walled pipes (>10mm) with high efficiency.
Applicable Scenarios:
- Large Structural Parts: Such as oil pipelines, ship frames, steel structure bridges.
- Thick-Walled Pipe Deformation Control: Multiple rollers distribute pressure to avoid localized stress.
Operating Steps:
- Position Heavy Pipe:
- Use lifting equipment to feed the pipe into the 7-roller system, ensuring horizontal alignment.
- Distribute Roller Pressure:
- Adjust hydraulic pressure for each roller to avoid overloading or pipe flattening.
- Segmental Rolling:
- Perform initial bending, then gradually increase pressure and complete large-radius shaping in multiple passes.
- Synchronized Control:
- All seven rollers operate in sync through a PLC system to ensure uniform motion and prevent twisting.
- Stress Relief:
- Post-bending, annealing (heat to ~600°C and slow cool) may be required to reduce residual stress.
Comparison Summary
Machine Type | Number of Rollers | Suitable Pipe Types | Advantages | Typical Applications |
3-Roller Bending | 3 | Small to medium pipes (≤150mm) | Simple structure, low cost | Guardrails, handrails, decorative parts |
5-Roller Bending | 5 | Precision thin-walled pipes (≤200mm) | Anti-wrinkle, high precision | Automotive exhaust pipes, aircraft conduits |
7-Roller Bending | 7 | Large thick-walled pipes (≥300mm) | Strong load capacity, suitable for heavy-duty pipes | Oil pipelines, ship structures |
Selection Recommendations
- Small batch / simple arc→ Use 3-roller machine (cost-effective and practical)
- High precision / thin-walled pipe→ Use 5-roller machine (better anti-deformation capability)
- Extra-large diameter / heavy industry→ Use 7-roller machine (multi-roller design distributes pressure evenly)
3.5Hot Bending (Induction Pipe Bending Machine)
Applicable Scenarios:Thick-walled pipes (≥6mm), large diameters (≥200mm), or special alloys.
Equipment:Medium-frequency induction pipe bending machine (includes induction coil and cooling system).
Operating Steps:
- Mark Heating Zone: Mark the bending section (width ≈ 3× pipe diameter).
- Localized Heating: Energize the induction coil to heat the zone to 900–1100°C (orange-red).
- Bending: Hydraulic arm pushes the heated section around a fixed die while water cooling solidifies the shape.
- Annealing (if needed): Heat the entire pipe to ~500°C and cool slowly to relieve internal stress.
4.0Considerations for Bending Stainless Steel Tubing
When planning a stainless steel tube bending process, several key factors must be taken into account to ensure dimensional accuracy and structural integrity. The most critical considerations include:
4.1Key Control Process
Material Evaluation→Calculate Minimum Bend Radius→Select Equipment & Dies →Set Process Parameters (Speed/Temp) →Apply Anti-Deformation Measures →Trial Bend & Adjustment →Post-Treatment & Inspection
4.2Material Characteristics
1. Stainless Steel Grades:
Austenitic (e.g., 304, 316): Prone to work hardening; control bending speed to prevent cracking.
Martensitic (e.g., 410): High hardness; may require preheating (hot bending recommended).
2. Diameter-to-Thickness Ratio (D/t):
Thin-walled pipe (D/t ≥ 20): Easy to collapse; support with mandrel or sand fill.
Thick-walled pipe (D/t ≤ 10): Requires greater bending force.
Bend angle |
Tube OD,in | ||||
1/4 | 1/4 | 5/16 | 3/8 | 1/2 | |
Bend Radius,in | |||||
9/16 | 3/4 | 15/16 | 15/16 | 11/2 | |
30° | 0 | 0 | 0 | 0 | 1/16 |
45° | 1/16 | 1/16 | 1/16 | 1/16 | 1/16 |
50° | 1/16 | 1/16 | 1/16 | 1/16 | 1/8 |
55° | 1/16 | 1/16 | 1/8 | 1/8 | 1/8 |
60° | 1/8 | 1/16 | 1/8 | 1/8 | 3/16 |
65° | 1/8 | 1/8 | 3/16 | 3/16 | 1/4 |
70° | 1/8 | 1/8 | 3/16 | 3/16 | 5/16 |
75° | 3/16 | 3/16 | 1/4 | 1/4 | 3/8 |
80° | 3/16 | 3/16 | 5/16 | 5/16 | 7/16 |
85° | 1/4 | 1/4 | 3/8 | 3/8 | 9/16 |
90° | 5/16 | 5/16 | 7/16 | 7/16 | 11/16 |
Stainless Steel Tubing Bend Radius Chart
4.3Bending Radius
Minimum Bend Radius (R):
Cold bending: R ≥ 1.5 × pipe diameter
Hot bending: R ≥ 1.0 × pipe diameter
Smaller radii may cause thinning or wrinkling
Empirical Formula:R = K × D (K is a material constant; for 304 stainless, K ≈ 2–3)
4.4Bending Speed & Temperature
Cold Bending:Slow speed recommended (hydraulic: 5–10°/s) to avoid cracking due to work hardening
Hot Bending:
- Heating temperature: 900–1100°C for austenitic stainless steel
- Ensure even heating to prevent localized overheating
- Sufficient soaking time for thick-walled pipes
4.5Anti-Deformation Measures
Mandrel Selection:
Rigid mandrel (steel): For high-precision bends
Flexible mandrel (ball chain type): For complex elbows
Mandrel tip should be 1–2mm ahead of the bend point to compensate for springback
Support Methods:
Fill thin-walled pipes with rosin, low-melting alloy, or sand (especially during hot bending)
Use wrinkle-suppressing dies (pressure pads) to control inner wall wrinkling
4.6Die & Equipment Parameters
Die Matching:
- Groove radius of bending die must match pipe OD (tolerance ±0.1mm)
- Excessive clearance can lead to oval deformation
Clamping Force:Hydraulic clamp pressure ≥ 1.5× pipe’s yield strength
Springback Compensation:
- Stainless steel springback: typically 2–5°
- Overbend via mold or CNC program correction
4.7Lubrication & Surface Protection
Lubricant:
- High-viscosity grease or MoS₂-based paste to reduce friction
- Avoid chlorine-containing lubricants (causes stress corrosion)
Surface Protection:Apply PE film or high-temp anti-oxidation coating during hot bending to avoid scratches and scaling
4.8Post-Processing Requirements
Stress Relief:Cold-bent stainless steel should be annealed at 300–400°C (especially for thick-walled pipes)
Roundness Correction:If ovality >5%, use mechanical expander or hydraulic forming to restore circular shape
5.0Common Problems & Solutions
Problem | Cause | Solution |
Outer wall cracking | Wall thinning >20%, or excessive speed | Increase bend radius, reduce speed, or hot bend |
Inner wall wrinkling | No mandrel or inadequate support | Use mandrel or anti-wrinkle pressure pad |
Oval deformation | Die gap too large | Use matched dies or increase clamping force |
Excessive springback | High elastic modulus of material | Design overbend or apply multi-stage correction |
References: