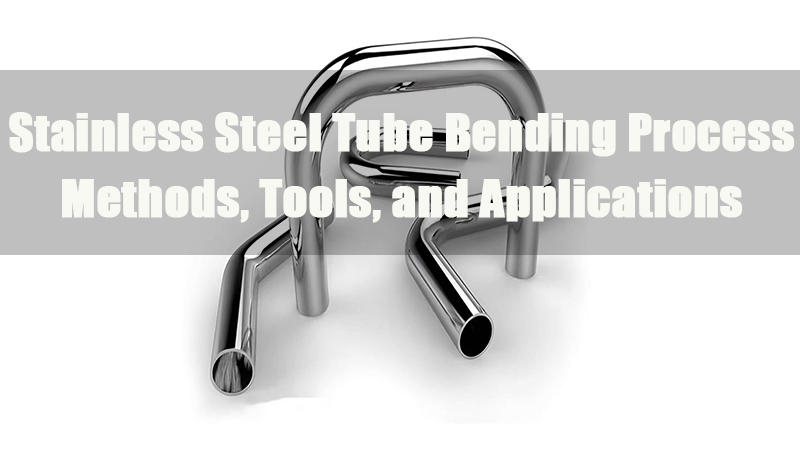
1.0스테인리스 스틸 튜브 굽힘 공정 소개
1.1스테인리스 스틸 소재 특성 및 굽힘 적응성
스테인리스강은 높은 강도, 내식성, 뛰어난 연성으로 인해 산업 제조에 있어 중요한 소재입니다.
단단하지만 형성 가능: 적절한 공정을 거치면 스테인리스강을 복잡한 모양으로 구부릴 수 있어 맞춤형 프로토타입과 정밀 부품에 적합합니다.
산업적 이점:
- 내구성: 부식 및 산화 저항성이 뛰어나 혹독한 환경에 적합합니다.
- 탄력성과 강도: 구조적 안정성과 성형 유연성을 모두 제공합니다.
1.2 스테인리스 스틸 튜브 벤딩의 주요 산업 응용 분야
산업 | 일반적인 응용 프로그램 | 프로세스 요구 사항 |
자동차 | 배기 파이프, 섀시 프레임, 연료 라인 | 고정밀 굽힘, 스프링백 제어, 고온 저항성 |
의료 | 수술 도구 브래킷, 의료용 튜빙 | 멸균 표면 마감, 소반경 정밀 굽힘 |
건설 | 난간, 장식 구조물, 커튼월 지지대 | 높은 미적 요구, 흔적 없는 굽힘 |
에너지 | 석유 파이프라인, 원자력 부품 | 두꺼운 벽 튜브 굽힘, 응력 부식 저항성 |
2.0스테인리스 스틸 튜브 벤딩의 과제와 해결책
2.1재료 특성 및 굽힘 어려움
- 높은 강도와 연성:스테인리스강은 높은 강도와 좋은 연성을 겸비하고 있어 구조용 부품과 산업 장비에 적합합니다.
- 도전 과제:고강도 → 더 큰 굽힘력이 필요하여 기계 부하가 증가합니다. 높은 연성 → 스프링백이 발생하기 쉽고 성형 정밀도에 영향을 미칩니다.
- 부식 저항성:굽힘 작업 중 표면이 손상되면(예: 긁힘, 움푹 들어간 부분) 부식 저항성이 떨어질 수 있으므로 과도한 마찰은 피해야 합니다.
2.2스테인리스 스틸 등급 간 가공 차이
스테인리스 스틸 타입 | 처리 기능 | 굽힘 과제 | 제안된 솔루션 |
304 스테인리스 스틸 | 연성이 좋아 널리 사용됨 | 상당한 스프링백, 반경 제어가 필요합니다. | – 스프링백 보정 다이 설계 – 약간 굽히세요(+2°~5°) |
316 스테인리스 스틸 | 몰리브덴 첨가로 내식성이 강하지만 단단함 | 더 많은 힘이 필요하고 작업 경화가 발생하기 쉽습니다. | – 고톤수 유압/CNC 튜브 벤더 사용 – 굽힘 속도 감소 |
듀플렉스 스테인리스 스틸 | 강도가 높고 인성이 좋으나 가공이 어려움 | 균열 발생이 쉽고 스프링백 제어가 복잡함 | – 예열 (200~300°C) – 점진적인 다중 패스 굽힘을 사용하세요 |
3.0굽힘 공정 방법 개요
스테인리스강 튜브 벤딩은 다양한 방법으로 가능하며, 각 방법은 특정 파이프 크기, 재료 특성 및 정밀도 요건에 맞춰 조정됩니다. 적절한 공정 선택은 성형 정확도, 표면 마감 및 구조적 신뢰성에 직접적인 영향을 미칩니다.
이 섹션에서는 수동, 유압, CNC, 롤 벤딩, 핫 벤딩 등 5가지 일반적인 벤딩 기술을 소개하고, 각 기술의 적합한 응용 분야, 장비 유형, 표준 작업 단계를 강조합니다.
3.1수동 파이프 벤딩(수동 파이프 벤더)
적용 가능한 시나리오:소량 생산, 소구경 파이프(일반적으로 ≤25mm), 정밀도 요구 사항 낮음.
장비:수동 파이프 벤더(다양한 크기의 다이 포함).
작동 단계:
- 주사위를 선택하세요:파이프의 외경(OD)에 따라 적합한 굽힘 다이를 선택하세요.
- 파이프를 고치세요:파이프를 벤더에 삽입하고, 한쪽 끝이 위치 지정 블록에 닿고 벤딩 시작점이 다이 중심과 일치하는지 확인합니다.
- 굽힘 위치 표시:마커를 사용하여 구부리기가 시작되어야 하는 위치를 표시하세요.
- 수동 조작:핸들을 천천히 당겨 파이프를 다이 주위로 원하는 각도로 구부립니다(각도 척도 참조).
- 스프링백 보상:스테인리스 스틸은 탄성이 있으므로, 스프링백을 상쇄하기 위해 약간 굽히십시오(2°~5°).
- 파이프 제거:클램프를 풀고 굽힘 각도와 둥글림을 확인하세요.
3.2유압 파이프 벤딩(유압 파이프 벤딩 머신)
적용 가능한 시나리오:중대형 파이프(DN15~DN150), 중간에서 높은 정밀도 요구 사항.
장비:유압 파이프 벤딩 머신(유압 펌프, 다이, 클램핑 장치 포함).
작동 단계:
- 다이 설치:파이프 직경에 맞게 벤딩 다이, 클램핑 다이, 가압 다이를 설치합니다.
- 매개변수 설정:굽힘 각도(예: 90°)와 속도를 설정합니다(속도를 낮추면 주름이 생기는 것을 방지할 수 있습니다).
- 파이프를 고치세요:파이프를 기계에 넣고 클램핑 다이로 고정하고 파이프 끝이 굽힘 다이와 일직선이 되도록 합니다.
- 유압 펌프 시작:버튼을 눌러 유압 실린더를 작동시키고, 유압 실린더가 굽힘 다이를 축을 중심으로 회전시켜 파이프를 구부립니다.
- 유지 압력:탄력을 줄이려면 2~3초간 압력을 유지하세요.
- 파이프 재설정 및 제거:유압 시스템을 해제하고 파이프를 제거한 후 움푹 들어간 부분이나 타원형 변형이 있는지 확인하세요.
3.3CNC 파이프 벤딩(CNC 파이프 벤딩 머신)
적용 가능한 시나리오:복잡한 3D 굽힘, 대량 생산, 고정밀(예: 자동차 배기 시스템).
장비:CNC 파이프 벤딩 머신(PLC 제어 시스템을 갖춘 서보 모터 구동).
작동 단계:
- 프로그램 작성: 제어판을 통해 굽힘 매개변수(각도, 반경, 이송 속도)를 입력하거나 CAD 도면을 가져옵니다.
- 파이프 고정: 파이프를 로딩 랙에 넣으면 기계가 자동으로 파이프를 고정하고 정렬합니다.
- 자동 굽힘:
- 클램핑 다이는 파이프를 제자리에 고정하고, 굽힘 다이는 프로그램에 따라 회전합니다.
- 맨드럴은 파이프 붕괴를 방지하고 부스터는 주름 발생을 방지합니다.
- 각 굽힘 후, 공급 장치는 파이프를 다음 굽힘 지점으로 이동합니다.
- 실시간 모니터링: 레이저 센서는 실제 굽힘 각도를 모니터링하고 스프링백을 자동으로 보정합니다.
- 제품 출력: 굽힘 작업 후 파이프는 자동으로 배출되어 품질 검사(예: 통과 게이지 테스트)를 실시합니다.
3.4롤 벤딩
3롤러 벤딩 머신
구조적 특징: 3롤러 레이아웃: 상부 롤러 1개(활성 프레싱 롤러) + 하부 롤러 2개(고정 지지 롤러).
조정 방법: 위쪽 롤러는 수직으로 움직이고, 아래쪽 롤러는 간격이 고정되어 있거나 조절 가능합니다.
적용 가능한 시나리오:
- 파이프 유형: 스테인리스 스틸 원형 파이프, 사각 튜브, 평강 등(적당한 벽 두께).
- 굽힘 반경: 대반경 호(예: 가드레일, 난간, 원형 구조물)에 적합합니다.
작동 단계:
- 상부 롤러 압력 조정: 파이프 직경과 벽 두께에 따라 상부 롤러의 하향 압력을 설정합니다.
- 파이프 공급 및 정렬: 파이프를 3개의 롤러 사이에 끼우고 시작 부분이 롤러와 일치하는지 확인합니다.
- 초기 사전 굽힘:
- 기계를 작동시킵니다. 위쪽 롤러가 아래로 눌리고 파이프가 굴러가며 초기 곡선을 형성합니다.
- 파이프 끝이 구부러지지 않은 경우(직선 모서리 효과로 인해), 필요한 경우 다이를 사용하여 끝을 미리 구부립니다.
- 점진적 굽힘:
- 목표 아크가 달성될 때까지 상부 롤러 압력을 점진적으로 조절하면서 롤링 패스를 반복합니다.
- 원형도 확인: 아크 템플릿이나 레이저 측정 장치를 사용하여 굽힘의 일관성을 확인하세요.
5롤러 벤딩 머신
5롤러 레이아웃: 고정된 하부 롤러 2개(지지대) + 측면 롤러 2개(가이드) + 상부 롤러 1개(활성 프레싱).
장점: 3롤러 설계보다 더욱 안정적이며, 고정밀, 복잡한 아크 벤딩에 적합합니다.
적용 가능한 시나리오:
- 높은 정밀도 요구 사항: 자동차 배기관, 항공기 배관, 정밀 기계 부품 등입니다.
- 얇은 벽 파이프 주름 방지: 측면 롤러는 변형을 줄이고 움푹 들어간 부분을 방지합니다.
작동 단계:
- 롤러 간격 조정:
- 파이프 직경에 따라 하단 및 측면 롤러의 위치를 설정하여 중앙 정렬을 보장합니다.
- 사전 굽힘 끝(선택 사항):
- 파이프 끝을 구부려야 하는 경우, 다이스나 유압 프레스를 사용하여 사전 구부립니다.
- 파이프 공급 및 정렬:
- 파이프를 5롤러 시스템에 삽입하고 모든 롤러와 균일하게 접촉하도록 합니다.
- 프로그레시브 롤링:
- 위쪽 롤러가 눌러주고, 옆쪽 롤러가 안내해주며, 반복적인 압연을 통해 파이프가 형성됩니다.
- 동적 조정:
- 실시간으로 굽힘 반경을 모니터링하고, 측면 롤러 압력을 미세 조정하여 스프링백을 제어합니다.
- 최종 검사: 진원도, 호의 매끄러움, 치수 허용 오차를 점검합니다.
7롤러 벤딩 머신
7롤러 레이아웃:
하부 롤러 3개(주 지지대) + 측면 롤러 2개(가이드) + 상부 롤러 2개(프레싱).
장점: 높은 효율성으로 특대 직경(>300mm)이나 두꺼운 벽의 파이프(>10mm)에 이상적입니다.
적용 가능한 시나리오:
- 대형 구조 부품: 석유 파이프라인, 선박 프레임, 철구조 교량 등입니다.
- 두꺼운 벽의 파이프 변형 제어: 여러 개의 롤러가 압력을 분산시켜 국부적인 응력을 방지합니다.
작동 단계:
- 무거운 파이프 위치:
- 리프팅 장비를 사용하여 파이프를 7롤러 시스템에 넣고 수평 정렬을 보장합니다.
- 롤러 압력 분배:
- 과부하나 파이프 납작해짐을 방지하기 위해 각 롤러의 유압을 조정하세요.
- 세그먼트 롤링:
- 초기 굽힘 작업을 수행한 다음, 점차 압력을 높이고 여러 차례에 걸쳐 대반경 성형을 완료합니다.
- 동기화된 제어:
- 7개의 롤러는 모두 PLC 시스템을 통해 동기화되어 작동하여 균일한 움직임을 보장하고 꼬임을 방지합니다.
- 스트레스 해소:
- 굽힘 가공 후에는 잔류 응력을 줄이기 위해 어닐링(약 600°C로 가열하고 천천히 냉각)이 필요할 수 있습니다.
비교 요약
기계 유형 | 롤러 수 | 적합한 파이프 유형 | 장점 | 일반적인 응용 프로그램 |
3롤러 벤딩 | 3 | 소형~중형 파이프(≤150mm) | 간단한 구조, 저렴한 비용 | 가드레일, 난간, 장식부품 |
5롤러 벤딩 | 5 | 정밀 박육관(≤200mm) | 주름방지, 고정밀 | 자동차 배기관, 항공기 배관 |
7롤러 벤딩 | 7 | 대형 두꺼운 벽의 파이프(≥300mm) | 강력한 하중 용량으로 중량물 파이프에 적합 | 석유 파이프라인, 선박 구조물 |
선택 권장 사항
- 소량 배치/단순 아크→ 사용 3롤러 머신 (비용 효율적이고 실용적)
- 고정밀/얇은벽파이프→ 사용 5롤러 머신 (더 나은 변형 방지 기능)
- 초대형 직경 / 중공업→ 사용 7롤러 머신 (멀티 롤러 디자인으로 압력을 고르게 분산)
3.5핫 벤딩(유도 파이프 벤딩 머신)
적용 가능한 시나리오:두꺼운 벽의 파이프(≥6mm), 대구경(≥200mm) 또는 특수 합금.
장비:중주파 유도관 굽힘 기계(유도 코일 및 냉각 시스템 포함).
작동 단계:
- 가열 구역 표시: 굽힘 부분을 표시하세요(너비 ≈ 3× 파이프 직경).
- 국소 난방: 유도 코일에 전원을 공급하여 해당 영역을 900~1100°C(주황색-빨간색)로 가열합니다.
- 굽힘: 유압 암이 가열된 부분을 고정된 금형 주위로 밀어내는 동안 수냉식으로 모양을 굳힙니다.
- 어닐링(필요한 경우): 파이프 전체를 약 500°C로 가열한 후 천천히 식혀서 내부 응력을 완화합니다.
4.0스테인리스 스틸 튜브 굽힘에 대한 고려 사항
스테인리스강 튜브 벤딩 공정을 계획할 때는 치수 정확성과 구조적 무결성을 보장하기 위해 몇 가지 핵심 요소를 고려해야 합니다. 가장 중요한 고려 사항은 다음과 같습니다.
4.1키 제어 프로세스
재료 평가→최소 굽힘 반경 계산→장비 및 다이 선택 →프로세스 매개변수 설정(속도/온도) →변형 방지 조치 적용 →시험 굽힘 및 조정 →후처리 및 검사
4.2재료 특성
1. 스테인리스 스틸 등급:
오스테나이트계 (예: 304, 316): 가공 경화되기 쉽습니다. 균열을 방지하려면 굽힘 속도를 조절하세요.
마르텐사이트 (예: 410): 경도가 높아 예열이 필요할 수 있습니다(열간 굽힘 권장).
2. 직경 대 두께 비율(D/t):
얇은 벽의 파이프(D/t ≥ 20): 붕괴하기 쉬움; 맨드렐이나 모래로 채워서 지지하세요.
두꺼운 벽의 파이프(D/t ≤ 10): 더 큰 굽힘력이 필요합니다.
만곡부 각도 |
튜브 OD,인 | ||||
1/4 | 1/4 | 5/16 | 3/8 | 1/2 | |
만곡부 반경, | |||||
9/16 | 3/4 | 15/16 | 15/16 | 11/2 | |
30° | 0 | 0 | 0 | 0 | 1/16 |
45° | 1/16 | 1/16 | 1/16 | 1/16 | 1/16 |
50° | 1/16 | 1/16 | 1/16 | 1/16 | 1/8 |
55° | 1/16 | 1/16 | 1/8 | 1/8 | 1/8 |
60° | 1/8 | 1/16 | 1/8 | 1/8 | 3/16 |
65° | 1/8 | 1/8 | 3/16 | 3/16 | 1/4 |
70° | 1/8 | 1/8 | 3/16 | 3/16 | 5/16 |
75° | 3/16 | 3/16 | 1/4 | 1/4 | 3/8 |
80° | 3/16 | 3/16 | 5/16 | 5/16 | 7/16 |
85° | 1/4 | 1/4 | 3/8 | 3/8 | 9/16 |
90° | 5/16 | 5/16 | 7/16 | 7/16 | 11/16 |
스테인리스 스틸 튜빙 굽힘 반경 차트
4.3굽힘 반경
최소 굽힘 반경(R):
냉간 굽힘: R ≥ 1.5 × 파이프 직경
열간 굽힘: R ≥ 1.0 × 파이프 직경
반경이 작으면 얇아지거나 주름이 생길 수 있습니다.
경험적 공식:R = K × D (K는 재료 상수입니다. 304 스테인리스의 경우 K ≈ 2–3)
4.4굽힘 속도 및 온도
냉간 굽힘:작업 경화로 인한 균열을 방지하기 위해 느린 속도(유압: 5~10°/s)를 권장합니다.
핫 벤딩:
- 가열 온도: 오스테나이트계 스테인리스 강의 경우 900~1100°C
- 국부적인 과열을 방지하기 위해 균일한 가열을 보장합니다.
- 두꺼운 벽의 파이프에 충분한 침지 시간
4.5변형 방지 조치
맨드렐 선택:
강성 맨드럴(강철): 고정밀 굽힘을 위해
유연한 맨드럴(볼 체인 타입): 복잡한 팔꿈치의 경우
스프링백을 보상하기 위해 맨드렐 팁은 굽힘 지점보다 1~2mm 앞서 있어야 합니다.
지원 방법:
얇은 벽의 파이프에 로진, 저용융 합금 또는 모래를 채웁니다(특히 열간 굽힘 작업 시)
주름 억제 다이(압력 패드)를 사용하여 내부 벽 주름을 제어합니다.
4.6금형 및 장비 매개변수
다이 매칭:
- 굽힘 다이의 홈 반경은 파이프 OD와 일치해야 합니다(허용 오차 ±0.1mm)
- 과도한 클리어런스는 타원 변형으로 이어질 수 있습니다.
클램핑 힘:유압 클램프 압력 ≥ 1.5× 파이프 항복 강도
스프링백 보상:
- 스테인리스 스틸 스프링백: 일반적으로 2–5°
- 금형 또는 CNC 프로그램 수정을 통한 오버벤드
4.7윤활 및 표면 보호
윤활유:
- 마찰을 줄이기 위한 고점도 그리스 또는 MoS₂ 기반 페이스트
- 염소가 함유된 윤활유는 피하세요(응력 부식을 유발합니다)
표면 보호:열간 굽힘 작업 시 긁힘 및 스케일 발생을 방지하기 위해 PE 필름 또는 고온 산화 방지 코팅을 적용합니다.
4.8후처리 요구 사항
스트레스 해소:냉간 굽힘 스테인리스강은 300~400°C에서 열처리해야 합니다(특히 두꺼운 벽의 파이프의 경우)
원형도 보정:타원도가 5% 이상인 경우 기계적 팽창기나 유압 성형기를 사용하여 원형 모양을 복원합니다.
5.0일반적인 문제 및 해결책
문제 | 원인 | 해결책 |
외벽 균열 | 벽 얇아짐 >20% 또는 과도한 속도 | 굽힘 반경을 늘리거나 속도를 줄이거나 핫 벤딩을 합니다. |
내벽 주름 | 맨드렐이 없거나 지지력이 부족함 | 맨드렐이나 주름 방지 압력 패드를 사용하세요 |
타원형 변형 | 다이 갭이 너무 큽니다 | 매칭된 다이를 사용하거나 클램핑력을 높이세요 |
과도한 스프링백 | 재료의 높은 탄성 계수 | 오버벤드를 설계하거나 다단계 보정을 적용하세요 |
참고문헌: