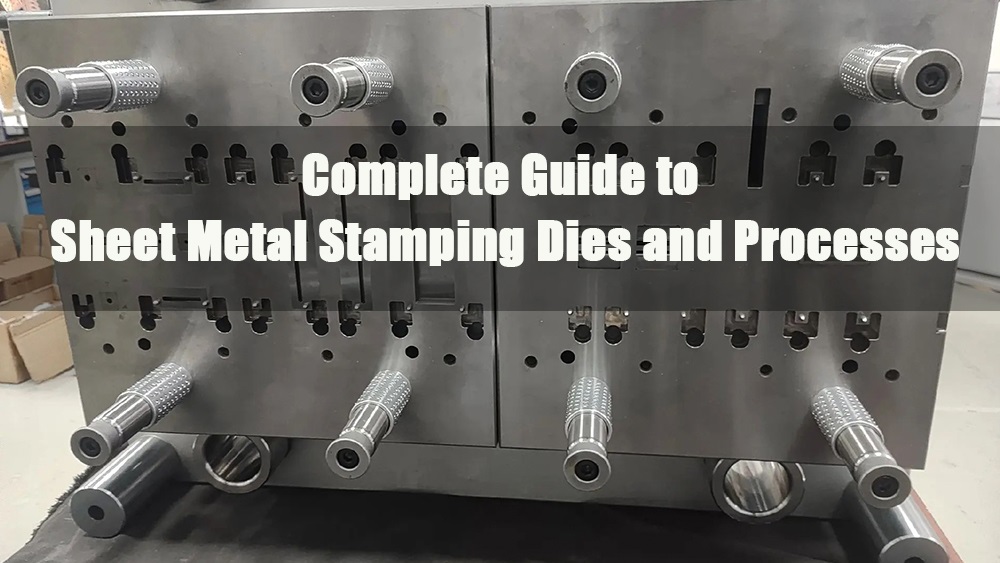
판금 스탬핑은 특수 다이와 강력한 프레스를 사용하여 금속판을 정밀한 부품으로 성형하고 절단하는 대량 생산 공정입니다. 자동차, 항공우주, 가전제품 등의 산업에서 널리 사용되는 이 공정은 소재의 성형성과 엔지니어링 툴링을 결합하여 복잡한 부품을 효율적으로 생산합니다.
1.0판금 스탬핑 및 다이 소개
판금 스탬핑은 다음을 사용하는 대량 생산 공정입니다. 스탬핑 프레스 판금을 완성된 부품으로 성형하고 절단하는 특수 다이. 프레스는 다이 세트를 닫는 데 필요한 힘을 전달하여 부품을 성형합니다.
생산 스탬핑은 일반적으로 두께가 0.020인치에서 0.080인치에 이르는 판금 소재를 사용하여 수행되지만, 이 공정은 매우 얇은 호일(0.001인치)과 두께가 1,000인치에 달하는 두꺼운 판재에도 적용될 수 있습니다.
2.0판금의 성형성과 연성 이해
성형성은 판금 소재가 스탬핑에서 얼마나 잘 작동하는지를 결정하는 주요 특성입니다. 이는 소재가 원하는 모양으로 구부리거나, 늘리거나, 잡아당길 수 있는 능력을 의미합니다. 이러한 특성은 야금학 용어로 "성형성"에 속합니다. 연성는 재료가 파괴되지 않고 변형되고 늘어날 수 있는 능력입니다. 부품의 형상과 복잡성은 재료가 얼마나 변형되어야 하는지에 직접적인 영향을 미칩니다.
재료 특성 외에도 다음과 같은 다른 요소도 성형성에 영향을 미칩니다.
- 다이의 디자인
- 프레스의 종류와 기능
- 프레스 스트로크 속도
- 윤활 방법
- 판금 공급 메커니즘
- 모니터링 및 제어 시스템
3.0판금 스탬핑 다이: 구성 요소 및 기능
다이는 모든 프레스 스트로크에서 일관되고 정확한 결과를 제공하도록 주의 깊게 설계되었습니다.
4.0다이 절단 및 블랭킹 작업
절단 다이는 판금을 원하는 모양으로 깎는 데 사용됩니다. 다음과 같은 몇 가지 특정 작업을 수행합니다.
- 블랭킹: 시트에서 부품의 전체 외부 프로필을 절단합니다.
- 펀칭: 슬러그를 제거하여 구멍이나 슬롯을 형성합니다.
- 트리밍: 성형된 부품에서 여분의 금속을 절단합니다.
이러한 작업에서는 펀치(수)와 다이(암) 사이의 적절한 다이 간극이 매우 중요합니다. 이 간극은 소재의 두께와 강도에 따라 결정됩니다. 일반적으로 소재가 두껍거나 단단할수록 간극은 더 넓어야 합니다. 금속이 연할수록 펀치가 더 깊이 관통할 수 있습니다.
5.0성형 다이 및 주요 작업
성형은 절삭이 아닌 다이의 윤곽을 기반으로 금속을 형상화하는 것을 의미합니다. 일반적인 성형 작업은 다음과 같습니다.
- 그림: 블랭크를 다이 캐비티에 넣어 깊은 모양을 만드는 작업입니다. 이 작업에는 블랭크 홀더 금속의 흐름을 제어하고 주름이나 파손을 방지합니다.
- 굽힘: 강성과 형태를 추가하기 위해 정의된 각도나 곡선을 생성합니다.
- 플랜징: 강도를 높이거나 고정하기 위해 가장자리에서 작은 각진 확장을 형성합니다.
- 헤밍: 플랜지 위로 접어서 맞물리는 부품의 매끄러운 모서리를 만듭니다.
각각의 성형 작업은 최종 부품의 전반적인 기하학, 강도, 기능에 영향을 미칩니다.
6.0단일 스테이션 및 다중 스테이션 다이
스탬핑 작업은 다양한 유형의 다이를 사용하여 수행할 수 있습니다.
- 단일 스테이션 다이:
- 복합 다이: 블랭킹, 펀칭 등 여러 절단 작업을 동시에 수행
- 조합 다이: 하나의 다이에서 절단과 성형을 모두 결합
다중 스테이션 다이:
- 프로그레시브 다이스: 코일 공급 소재를 사용하고, 각 스테이션은 스탬핑 공정의 각 단계를 수행합니다. 부품은 완전히 성형되고 분리될 때까지 캐리어 스트립을 통해 연결된 상태로 유지됩니다.
- 전송 다이: 동일한 다이 세트 내에서 스테이션 간에 기계적으로 전송되는 사전 절단된 블랭크를 사용합니다.
- 탠덤 프레스 라인: 시리즈의 각 프레스가 특정 작업(예: 드로잉 또는 트리밍)을 수행하는 대규모 작업
이러한 다양한 다이 구성을 통해 복잡한 부품을 효율적이고 높은 처리량으로 생산할 수 있습니다.
7.0스탬핑에서 다이 윤활의 중요성
스탬핑 작업 중 공구와 금속 소재 사이의 고압 접촉으로 인해 상당한 마찰이 발생합니다. 윤활은 이러한 마찰을 줄여 공구 수명을 향상시키고, 필요 중량을 줄이며, 표면 조도를 향상시킵니다.
일반적인 윤활제 유형은 다음과 같습니다.
- 가벼운 미네랄 오일
- 고점도 드로잉 컴파운드
- 오일 기반, 수용성 또는 합성 윤활제
다음 방법을 통해 적용할 수 있습니다. - 수동 브러시 또는 롤러
- 드립 시스템
- 자동화된 기계 롤러
- 분무 또는 홍수 적용
성공적이고 일관된 성형 공정을 위해서는 올바른 윤활 방법과 유체를 선택하는 것이 필수적입니다.
8.0원형 그리드 분석(CGA): 스탬프 부품 품질 최적화
왜곡된 그리드를 분석함으로써 금형 제작자는 금형 수정이 필요한 부분을 파악할 수 있습니다. 이 과정은 최종 부품이 품질 요건을 충족할 때까지 반복됩니다.
9.0금형 설계에 유한 요소 모델링(FEM) 사용
시행착오에 소요되는 시간을 줄이기 위해 엔지니어들은 다음과 같은 시뮬레이션 도구를 점점 더 많이 사용합니다. 유한 요소 모델링(FEM)FEM을 사용하면 딥 드로잉과 같은 복잡한 성형 공정의 가상 분석을 통해 실제 금형 제작 전에 재료의 거동을 예측할 수 있습니다. 이는 다음과 같은 이점을 제공합니다.
- 툴링 재작업 최소화
- 빈칸 모양과 크기를 최적화하세요
- 금형 제작 전에 부품이 제조 가능한지 확인하십시오.
FEM은 CGA와 전문적인 기술을 결합하여 더욱 효율적인 스탬핑 워크플로와 더 높은 품질의 부품을 만들어냅니다.
10.0FAQ: 판금 스탬핑 및 다이
Q1: 판금 스탬핑에서 블랭킹과 펀칭의 차이점은 무엇입니까?
A1: 블랭킹은 시트에서 부품의 바깥쪽 둘레를 절단하는 작업이고, 펀칭은 부품 내부에 슬러그를 제거하여 구멍이나 개구부를 만드는 작업입니다. 두 작업 모두 다이를 사용하여 수행됩니다.
Q2: 진행형 다이와 전사형 다이의 차이점은 무엇입니까?
답변2: 프로그레시브 다이는 여러 다이 스테이션을 통해 코일 소재를 공급하며, 각 스테이션은 연속적인 스트립에서 서로 다른 작업을 수행합니다. 이송 다이는 기계적 이송 시스템을 사용하여 개별 블랭크를 한 스테이션에서 다른 스테이션으로 옮깁니다.
Q3: 펀칭 작업에서 다이 클리어런스가 왜 그렇게 중요한가요?
A3: 적절한 다이 클리어런스는 깨끗한 절단을 보장하고, 버(Burr)를 방지하며, 공구 마모를 줄여줍니다. 소재 두께와 소재 특성에 따라 다이 클리어런스를 조정해야 합니다.
Q4: 딥 드로잉 시 주름이나 찢어짐이 생기는 원인은 무엇인가요?
A4: 성형성 불량, 블랭크홀딩력 부족, 또는 잘못된 펀치/다이 설계는 주름, 얇아짐, 또는 찢어짐을 초래할 수 있습니다. 이러한 결함은 일반적으로 CGA 또는 FEM 분석을 통해 식별 및 수정됩니다.
Q5: 금속 스탬핑에는 어떤 유형의 윤활제를 사용해야 합니까?
A5: 윤활제 선택은 작업 유형과 재질에 따라 달라집니다. 가벼운 성형 작업에는 경유가 일반적으로 사용되는 반면, 고강도 인발 작업에는 고점도 합성유가 필요할 수 있습니다. 도포 방법 또한 효율에 영향을 미칩니다.
Q6: 하나의 주사위로 여러 작업을 수행할 수 있나요?
A6: 네. 복합 다이와 콤비네이션 다이는 블랭킹, 펀칭, 성형을 동시에 수행할 수 있습니다. 프로그레시브 또는 이송 시스템과 같은 다중 스테이션 다이는 별도의 스테이션을 통해 작업을 순차적으로 진행합니다.
Q7: 유한 요소 모델링은 금형 설계를 어떻게 개선합니까?
A7: FEM은 금형 제작 전에 재료 흐름과 변형을 시뮬레이션합니다. 잠재적인 고장 영역을 파악하고, 재작업을 줄이며, 부품을 정확하고 효율적으로 생산할 수 있도록 보장합니다.
참고문헌
https://www.tldmetal.com.tw/news_detail/21.htm