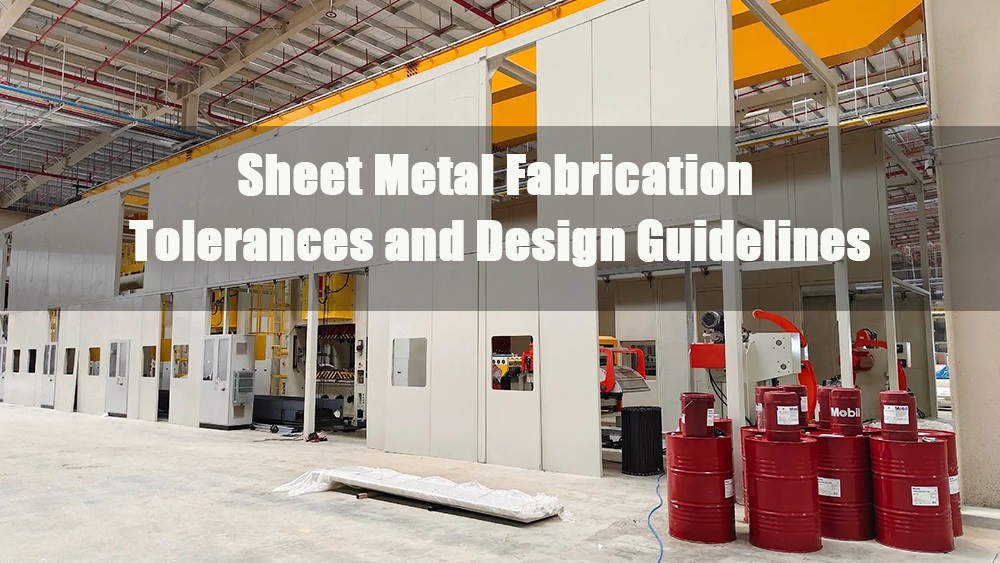
導入
板金加工公差は、加工部品のサイズ、形状、その他の特徴における許容偏差を定義します。これらの公差は、 正確な設置, 一貫した組み立て、 そして スムーズな統合 他のコンポーネントと。
ほとんどの場合、メーカーは ISO 2768-mk 制御する:
- 長さ寸法と角度寸法
- 平坦性と直線性
- 円筒度と真円度
以下のセクションでは、 標準許容差 そして 重要なデザインのヒント 正確かつ効率的な板金加工を実現します。
1.0板金加工の標準許容差
1.1金属スピニング公差(ISO 2768規格参照)
以下の表は、許容偏差(mm)を示しています。 ISO 2768異なる公称長さの範囲に基づいて:
公称サイズ範囲(mm) | 罰金(f) | 中(m) | 粗い(c) | 非常に粗い(動詞) |
0.5~3 | ±0.1 | ±0.2 | — | — |
3歳以上6歳未満 | ±0.05 | ±0.1 | ±0.3 | ±0.5 |
30歳以上120歳未満 | ±0.1 | ±0.2 | ±0.5 | ±1.0 |
120以上400まで | ±0.15 | ±0.3 | ±0.8 | ±1.5 |
400以上1000まで | ±0.2 | ±0.5 | ±1.2 | ±2.5 |
1000以上2000以下 | ±0.3 | ±0.8 | ±2.0 | ±4.0 |
2000以上4000まで | ±0.5 | ±1.2 | ±3.0 | ±6.0 |
1.2外径と面取り高さ
範囲(mm) | 罰金(f) | 中(m) | 粗い(c) | 非常に粗い(動詞) |
0.5~3 | ±0.2 | ±0.2 | ±0.4 | ±0.4 |
3歳以上6歳未満 | ±0.5 | ±0.5 | ±1.0 | ±1.0 |
6歳以上 | ±1.0 | ±1.0 | ±2.0 | ±2.0 |
1.3角度寸法公差
公称長さ(mm) | 罰金(f) | 中(m) | 粗い(c) | 非常に粗い(動詞) |
最大10 | ±1° | ±1° | ±1°30′ | ±2° |
10歳以上50歳未満 | ±0°30′ | ±0°30′ | ±1° | ±2° |
50歳以上120歳未満 | ±0°20′ | ±0°20′ | ±0°30′ | ±1° |
120以上400 | ±0°10′ | ±0°10′ | ±0°15′ | ±0°30′ |
400以上 | ±0°05′ | ±0°05′ | ±0°10′ | ±0°20′ |
2.0板金加工の設計ヒント
設計を最適化することで、製造コストを削減し、高品質な結果を得ることができます。以下は 重要な設計ガイドライン 標準的な DfM プラクティスと業界分析に基づいています。
2.1壁の厚さ
均一: 部品全体にわたって均一な壁厚を維持することは、構造の完全性と正確な組み立てにとって不可欠です。厚さが不均一だと、製造中に反り、位置ずれ、公差の問題が発生する可能性があります。
推奨厚さ範囲:
- 一般的な製造: 9~20 mm(通常3 mm以下のシートの場合、 せん断機 またはギロチン鋏。
- レーザー切断:高精度と最小限の熱歪みを実現する CNC レーザー切断機を使用する場合は、5 ~ 10 mm が理想的です。
- 曲げ: プレスブレーキマシンで一貫した結果を得るには5~6mmが推奨されます。 CNCプレスブレーキひび割れや過度のスプリングバックのない正確な曲げを保証します。
2.2ベンド
曲げ加工は板金加工において極めて重要な工程であり、部品の精度と全体的な品質に直接影響を及ぼします。適切なパラメータ設定により、材料の変形を最小限に抑え、公差を一定に保つことができます。ほとんどの曲げ加工は、曲げ角度と寸法を正確に制御できるプレスブレーキ機またはCNCプレスブレーキで行われます。
2.3Kファクター
- 意味: K係数は中立軸(t)と材料の厚さ(Mt)の比であり、次のように表されます。 K = t / Mt.
- 推奨範囲: 3 – 0.5(ほとんどの金属の平均は約0.4468)。
- 目的: K 係数を正確に計算すると、曲げ許容値とフラット パターンを決定するのに役立ち、破れや過度の材料の薄化を防止できます。 CNCプレスブレーキマシン プログラム可能な曲げ許容度計算機を使用すると、K 係数の値を自動的に調整して、再現性のある精度を実現できます。
2.4曲げ半径
- 意味: 曲げ半径は、曲げ軸と材料の内部表面間の距離です。
- ガイドライン:
- ステンレス鋼のような延性材料の場合、 内側の曲がり 半径 ひび割れを防ぐために、少なくとも材料の厚さと同じにする必要があります。
- 脆い金属(アルミニウム合金など)の場合、歪みや歪みを減らすために、曲げ半径を大きくすることが推奨されます。
- 装備のヒント: モダンな CNCプレスブレーキ 半径ツールを備えた製品は、複雑なコンポーネントでも一貫した曲げ半径を実現するのに最適です。
2.5曲げ方向
曲げ方向を一定に保つことで、部品の再方向付けの必要性が減り、生産コストが削減され、リードタイムが短縮されます。自動化 プレスブレーキマシン 多軸バックゲージを使用すると、手動調整がさらに最小限に抑えられ、生産全体にわたって均一な曲げ方向が保証されます。
2.6曲げ緩和
曲げリリーフを追加することは、エッジ付近の裂け目や変形を防ぐために不可欠です。
- 深さ: 曲げ半径より大きい。
- 幅: 少なくとも材料の厚さと同じ。
- 利点: 曲げリリーフは、特に高強度鋼で加工した場合、剛性を向上させ、スプリングバックを最小限に抑えます。 油圧プレスブレーキ または CNCサーボ電動プレスブレーキ.
2.7曲げ高さ
- 最小高さ: 少なくとも 2 × 材料の厚さ + 曲げ半径.
- 理由: 曲げ高さが小さすぎると、プレスブレーキでシートを正確に配置することが難しくなり、曲げ品質が低下したり、変形したりする可能性があります。 CNCプレスブレーキ 厳しい公差を維持しながら小さな曲げ高さを形成するには、精密なクランプ システムを備えたものが推奨されます。
2.8裾
ヘムは、鋭いエッジを排除し、安全性を高め、板金部品の構造的強度を高めるために使用されます。
- 一貫性: 同じ曲げ方向のガイドラインに従うことで、不要な部品の再方向付けを減らし、効率性を向上させることができます。 プレスブレーキマシン.
- 曲げ高さ: 一般的な曲げ高さの推奨値を満たす必要があります(≥2 × 材料の厚さ + 曲げ半径).
2.9穴のサイズと間隔
ガイドライン
- 直径: ≥ 材料の厚さ(工具の摩耗とコストを削減するためには、大きい方が望ましい)。
- 間隔: 板金の厚さの2倍以上。
- エッジ距離: 破れを防ぐために材料の厚さ以上で使用してください。
概要表
デザインの特徴 | 推奨値 |
最小穴径 | ≥ 材料の厚さ |
穴間隔 | ≥ 2 × 材料の厚さ |
エッジからの距離 | ≥ 材料の厚さ |
2.10カールと皿穴
カール
- 外側の半径: ≥ 2 × 材料の厚さ。
- カール付近の穴のサイズ: ≥ カール半径 + 材料の厚さ
皿穴
- 深さ: ≤ 0.6 × 材料の厚さ。
- 中心間の距離: ≥ 8 × 材料の厚さ。
- 曲げ線からの距離: ≥ 3 × 材料の厚さ。
2.11タブとノッチ
タブ
- 長さ: ≤ 5 × 幅。
- 幅: ≥ 2 × 材料の厚さ。
ノッチ
- 幅: ≥ 材料の厚さ。
- 間隔: ノッチの間隔は 1/8 インチ以上。
- 曲がり角への近さ: ≥ 3 × 金属の厚さ + 曲げ半径。
2.12板金ゲージの考慮事項
- 厚いシート: 達成可能な曲げ角度が制限され、微小亀裂が発生する可能性があります。
- 推奨される実践: 高い構造強度が必要でない限り、より薄く、より柔軟な金属を使用します。
3.0板金加工用材料
適切な材料を選ぶには 用途、強度、耐食性、加工性以下は一般的なオプションです。
3.1ステンレス鋼
プロパティ: 耐腐食性、耐久性、耐熱性、成形性に優れています。
アプリケーション:
- 調理器具
- 航空宇宙および自動車部品
- 食品加工機器
- 化学薬品および燃料容器
3.2熱間圧延鋼
プロパティ: 柔軟で展性があり、寸法公差がそれほど厳しくありません。
アプリケーション:
- 車両フレーム
- 農業機械
- 鉄道線路と車両部品
3.3冷間圧延鋼
プロパティ: 熱間圧延よりも強度が約20%、仕上げが滑らか。
アプリケーション:
- 自動車部品
- 家電製品
- 照明器具
3.4銅と真鍮
- 銅: 展性があり、耐腐食性があり、成形しやすい。
- 真鍮: 耐腐食性、高導電性、耐高温性。
- アプリケーション: 備品、電子機器、キッチン用品。
3.5プレメッキ鋼
- プロパティ: プレメッキ鋼、多くの場合、 デコイラーおよびストレートナーフィーダー ラインは、スタンピングおよび曲げ加工のスムーズな供給を保証します
- アプリケーション: 機器本体、筐体。
3.6アルミニウム
プロパティ: 軽量、強靭、耐腐食性、優れた熱伝導性、電気伝導性。
アプリケーション:
- 自動車および航空機部品
- 電気エンクロージャ
- 食品包装
4.0板金の表面仕上げオプション
4.1ビーズブラスト
- プロセス研磨粒子(砂またはガラスビーズ)を圧縮空気で吹き付けます。
- 長所: 滑らかでマットな質感、環境に優しく、敏感な表面に適しています。
- 短所: 高速ではないので、小規模プロジェクトには適していません。
4.2粉体塗装
- プロセス: 粉体塗料を吹き付けて焼き付け、保護層を形成します。
- 長所: 耐腐食性に優れ、長持ちし、経済的です。
- 短所: 色の混合が制限されており、少量生産の場合は高価になる可能性があります。
4.3陽極酸化処理
- 種類:
- タイプI:薄層、クロム酸
- タイプII:硫酸、耐腐食性
- タイプIII:ハードコート、耐摩耗性
- 長所: UV安定性、耐久性のある仕上げ
- 短所: 特定の金属に限定
4.4ブラッシング
- プロセス: フィラメントブラシがバリを取り除き、表面の滑らかさを向上させます。
- 長所耐久性と耐腐食性を向上
- 短所: 損傷を受けやすく、ブラシ跡が残る場合があります
4.5スクリーン印刷
- 使用: ロゴ、ラベル、安全に関する指示
- 長所: コスト効率が高く、色やサイズの制限はありません
- 短所: 精密な色合わせは難しい
4.6板金加工において公差管理が重要な理由
厳しい許容誤差を維持することで、次のことが保証されます。
- 正確な組み立てと設置
- 材料の無駄と手直しの削減
- 耐久性と性能の向上
- 生産コストの削減とリードタイムの短縮
5.0結論
適切な理解と適用 板金加工公差 確保するために重要です 高品質の部品, コスト効率、 そして 速い生産サイクルISO 2768規格に準拠し、 製造のための設計(DfM) 均一な壁の厚さ、正しい曲げ半径、適切な穴間隔を維持するなどの原則に従うことで、やり直しが減り、組み立て精度が向上し、製品寿命が延びます。
右と組み合わせると 材料の選択 そして 表面仕上げオプションこれらの実践は、メーカーが業界全体で一貫した結果を達成するのに役立ちます。 自動車, 航空宇宙, エレクトロニクス、 そして 産業機械.
6.0よくある質問(FAQ)
板金加工の標準許容差は何ですか?
ほとんどのメーカーは ISO 2768-mk線形寸法公差は、小さな部品の場合は ±0.05 mm、非常に大きな部品の場合は ±6.0 mm です。
板金曲げ加工に推奨される K 係数は何ですか?
の K係数 通常は 0.3から0.5平均は 0.4468 ほとんどの曲げ作業に使用できます。
壁の厚さは板金加工にどのような影響を与えますか?
板厚を厚くすると構造強度は向上しますが、曲げ角度が制限され、ひび割れのリスクが高まる可能性があります。板厚を薄くすると成形や曲げ加工が容易になりますが、構造剛性が低下する可能性があります。
耐腐食性に最適な材料は何ですか?
ステンレス鋼、アルミニウム、銅、真鍮 優れた耐食性を備えています。ステンレス鋼は食品、医療、化学業界で広く使用されています。
屋外での使用に最適な表面仕上げは何ですか?
粉体塗装 そして 陽極酸化処理 耐腐食性、耐紫外線性、耐候性が高いため、屋外での使用に最適です。