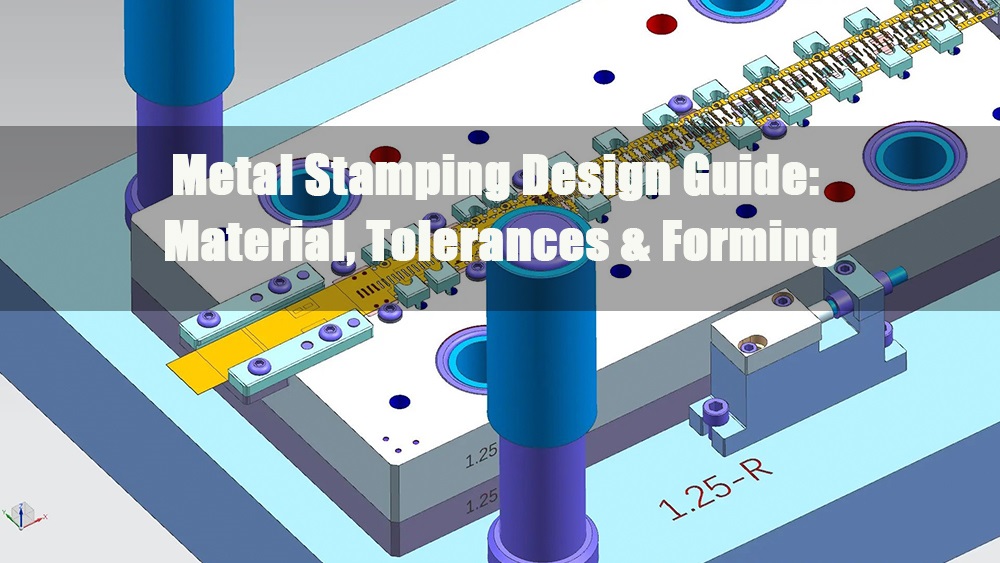
金属プレス加工は、安定した一貫した性能を備えた耐久性、強度、耐摩耗性に優れた部品を製造するための費用対効果の高い方法です。
このガイドでは、製造性、再現性、材料効率を最大限に高めるスタンプ部品の設計に役立つ包括的な洞察とベスト プラクティスを紹介します。
1.0プレス部品の材料選定
適切な金属板または帯板の選択は非常に重要です。材料によって価格、入手性、性能特性が大きく異なります。常に機械的特性と調達要因の両方を考慮してください。
- 在庫あり vs. カスタム在庫あり: 標準ゲージ サイズは一般的に在庫されており、コスト重視または短納期のアプリケーションでは優先する必要があります。
- 最小数量製鉄所では通常、カスタム厚さや合金鋼の注文にトラック1台分の数量が必要です。少量の場合は倉庫からの調達が有効な場合もありますが、在庫状況は変動します。
- 再ロールオプション: 専門の再ローラー業者は少量の要求を満たすことができますが、コストが大幅に増加します。
一般的な刻印材料の比較
材質タイプ | 強さ | 成形性 | 相対コスト | 一般的な用途 |
---|---|---|---|---|
軟鋼 | 中くらい | 高い | 低い | ブラケット、ハウジング、一般部品 |
ステンレス鋼 | 高い | 中くらい | 高い | 医療器具、器具 |
アルミニウム | 低い | 非常に高い | 中くらい | エンクロージャ、ヒートシンク |
真鍮 | 中くらい | 高い | 中高 | 電気接点、装飾 |
2.0金属プレス加工における公差の考慮
標準的な鋼種は、一定のゲージ厚と公差で提供されます。公差を狭めることは可能ですが、一般的にコストが上昇します。材料公差を指定する際は、以下の点にご注意ください。
- 固執する 業界標準のゲージ厚さ可能な場合は。
- 理解してください 厳しい許容範囲により調達の選択肢が制限される可能性がある特に非標準の材料仕様の場合。
- ゆるい 許容範囲 倉庫の在庫を活用できるようになり、コストとリードタイムが削減されます。
3.0材料化学:過剰な仕様設定を避ける
スタンプコストが高騰する主な原因の一つは 合金の過剰指定鉄系合金および非鉄系合金は数多く存在しますが、一般的に在庫されているのはごくわずかです。特殊合金は、多くの場合、大量に特注溶解する必要があります。
- 現代の 連続鋳造これにより、合金の一貫性と延性が大幅に向上しました。
- 使用を検討してください 倉庫 材料 許容範囲とアプリケーションが許す限りいつでも。
4.0ブランク、トリミング、穿孔技術
スタンピングにおける穴形成の理解
打ち抜きや穿孔などのスタンピング加工では、工具鋼製のパンチを金属に押し込み、金型に押し込みます。これにより、予測可能な刃先形状が得られます。
- あ 丸められたまたは丸みを帯びた上端 圧縮が始まると形成されます。
- あ 磨かれたまっすぐな壁 材料が剪断された場所に生成されます。
- 応力が材料の強度を超えると、 離脱する、形成する バリ一番下にあります。
打ち抜き部品のバリ管理
バリは、射出成形のパーティングラインと同様に、スタンピング加工の自然な結果です。バリの高さは最大で 10%の材料の厚さこれらは次のようになります:
- 化粧品以外の用途ではそのまま残します。
- 鈍くなったり 削除された 必要に応じて大量仕上げまたは二次加工を行います。
5.0穴とフィーチャの寸法公差
パンチとダイのクリアランス(通常、片側あたり8~10%の材料厚さ)により、次の問題が発生します。
- 内部機能(例:穴)テーパー 上部が広い.
- 外部機能(例:タブ)テーパー 下部が狭い.
デザイナーは次のことを行う必要があります。
- 寸法穴 最小/せん断直径.
- 寸法外側特徴 最大/せん断部分.
- 使用 シェービング 必要に応じて、直線エッジの加工を追加料金で行います。
材質別の標準許容差
材質タイプ | 共通ゲージ公差 | ピアス許容能力 |
---|---|---|
軟鋼 | ±0.005インチ | ±0.002インチ |
ステンレス鋼 | ±0.003インチ | ±0.0025インチ |
アルミニウム | ±0.004インチ | ±0.002インチ |
高強度合金 | ±0.006インチ | ±0.003インチ |
6.0精密穴位置公差
- 同一平面のピアス 精度は非常に高く、穴間の誤差は ±.002 インチが一般的です。
- 穴が 材料の厚さの1.5倍より近い、または 異なる飛行機スプリングバックと曲げの変動を考慮して、許容差を緩める必要があります。
- 密集した穴 精度を維持するために個別の操作が必要になる場合があります。
材質タイプ | 共通ゲージ公差 | ピアス許容能力 |
軟鋼 | ±0.005インチ | ±0.002インチ |
ステンレス鋼 | ±0.003インチ | ±0.0025インチ |
アルミニウム | ±0.004インチ | ±0.002インチ |
高強度合金 | ±0.006インチ | ±0.003インチ |
7.0金属プレス加工における金型設計ガイドライン
ツールは大きな力に耐えなければなりません:
- 0.062インチの軟鋼に0.5インチのパンチを打つには、通常2.5トンの圧力が必要で、 高速スタンピングプレス機.
- 毎分80個の部品生産を可能にするのは、 サーボフィーダー ストリップ金属を順送金型に高速で送り込むシステム。
パンチの破損を防ぐには:
- 穴やスロットを設計する 最小断面積 = 材料の厚さ.
- 鋭い内部コーナーや極端に薄いセクションを避けてください。
8.0プレス加工における曲げと成形
金属成形 スタンピングプレス 直線的な垂直方向の操作です。材料の成形性はその 合金と焼き入れ:
- 温度が低いほど延性が高くなる、形成しやすくなります。
- より硬い焼き入れ = より大きな反発、必要 過度に曲げる
経験則の形成:
- 90°曲げ 標準的ですが、より複雑な形状の場合は、追加のダイステーションが必要になるか、 CNC曲げ機 成形後の作業用。
- の 形成された脚 すべきだ 材料の厚さの2.5倍以上 曲げ半径を超えて、構造の完全性と再現性を確保します。
9.0歪みと曲げ欠陥の管理
材料が曲がる場合:
- の 内面が圧縮される; その 外面が伸びる.
- これにより、 壁の薄化, 膨らんだ、 または つまんだ角.
これを管理するには:
- 追加 救済穴 交差する曲げの基部(例:ボックスのコーナー)
- 輪郭ブランク 重要な部分での曲げの膨らみを回避するため。
- メモを追加する。 「このエリアでは膨らむことは禁止されています」 必要に応じて、図面に記入します。
10.0成形フィーチャの寸法と公差
曲げによって複数の変数が導入されます。
- 材料の厚さの許容差
- 角度曲げ許容範囲(±1°標準)
- ステーション間のツール精度
設計ガイドライン:
- 曲げの内側からの寸法外側の端からではなく、外側から。
- フィーチャが曲げから遠くに配置されている場合、 角度の変化 大きな寸法変化を引き起こす可能性があります。これは公差に考慮する必要があります。
- 複雑なフォームでは 適格性評価またはサイズ決定操作 正確性を維持するためです。
11.0深絞りスタンピング:設計とプロセスのガイドライン
ディープドローとは何ですか?
深絞りは、平らなブランクを丸いダイスで引っ張り、キャビティに挿入して、 底が閉じたシェル または 円筒形のカップストレッチ成形とは異なり、この素材は 引っ張られた、伸ばされていません。
深絞りのメカニズム
このプロセスには 2 つの段階があります。
- カッピング: パンチがブランクに接触して材料を引き伸ばし、 衝撃線(下部の半径の周りに目に見える薄さが見られます)。
- 描画: 物質的な壁 厚くなる(元の厚さの最大 +10%) が内側と下向きに流れます。
深絞り加工における設計上の意味合い
- の パンチはテーパー状にする必要がある部品の取り外しが可能になります。
- シェルは自然に先細りになる 下(狭い)から上(広い)まで。
- 材料の木目方向により、 丸くない貝殻.A フランジ 丸みを保つのに役立ちます。
- ピンチ トリミング 部分的に内側の半径を残し、外側のエッジを鋭角にしておきます。面一カットが重要な場合は、機械加工が必要です。
描画シェルの指定
厚さは描画によって変化するため、
次のいずれかを使用します。
- 材料の開始厚さ
- 最小壁厚
- 最大壁厚
寸法 ID(内径) パンチ寸法を参照する場合。
寸法 OD(外径) 最終製品を参照する際は、テーパ許容値に注意してください。
12.0金属プレス加工における平坦性
材料関連の歪み
コイル供給ストリップ金属には、主に 2 つの問題があります。
- コイルセット(縦方向に湾曲): 多くの場合、精密レベリング マシンまたはローラー平坦化システムを使用してコイルの縦方向の湾曲を修正し、真っ直ぐにすることができます。
- クロスボウ(幅方向に湾曲している): 除去が非常に困難で、最終的な平坦性に影響することがよくあります。
プロセス誘発歪み
打抜きおよび成形の応力により、特に以下の場合に材料のエッジが曲がったり丸まったりします。
- 厚い素材
- より硬い合金(例:ステンレス鋼、高強度鋼)
歪みを最小限に抑えるには:
- ミシン目を入れないようにする 近すぎる または 近くの端—厚さの1.5倍以上残してください。
- 穴を開ける 曲げや型枠から離れた部分の厚さの2倍以上.
- 不可能な場合は、 穴公差を拡大する 歪みを考慮するため。
13.0プレス部品の表面化粧管理
ツールマーク
高い力により、 工具跡は避けられない 多くの場合:
- ワイプ成形外側の曲げ部分に傷が残ります。
- 描画 原因 衝撃線.
- コイニングとエンボス加工 目に見える圧力の跡が残ります。
クリエイティブな金型設計と 微細工具表面 これらを最小限に抑えることができます。特に 外見は重要.
14.0取り扱いと表面保護
大半の刻印は次の通りです:
- バルク処理 生産ラインを通じて。
- 質量が完成しました(タンブリング、バリ取り等)。
- バルクパック多くの場合、個別の保護はありません。
敏感な部分の場合:
- 定義する 化粧品 要件 図面上。
- 考慮する 個別包装 または 最終仕上げ作業 表面の完全性が重要である場合。
15.0最後に
これらの金属プレス加工設計原理を理解し、適用することで、部品の品質を飛躍的に向上させ、生産コストを削減し、製造性の一貫性を確保できます。適切な材料の選択、深絞りの公差、形状に配慮した形状設計など、経験豊富な金型エンジニアやメーカーとの連携が最良の結果をもたらします。
16.0金属スタンピングデザインに関するよくある質問(FAQ)
1. 金属プレス加工に最適な材料は何ですか?
金属プレス加工で一般的に使用される材料には、炭素鋼、ステンレス鋼、アルミニウム、銅、真鍮などがあります。最適な材料は、強度、成形性、導電性、耐腐食性、コスト効率など、用途のニーズに応じて異なります。
2金属打ち抜き部品のバリを最小限に抑えるにはどうすればよいでしょうか?
バリは、打ち抜き加工やピアシング加工の際に発生する通常の副産物です。バリの高さを最小限に抑えるには、以下の手順を踏んでください。
- 最適なパンチ/ダイクリアランスを使用する(片側あたり約8~10%の材料厚さ)
- ツールの鋭さとメンテナンスを確保する
- 化粧品用途では、二次バリ取りやタンブリング作業を検討してください。
3. 打ち抜き金属部品に期待できる標準的な許容誤差はどのくらいですか?
高精度アプリケーションでは、穴やエッジの標準寸法公差は±0.002インチに抑えられることが多いです。ただし、以下の要因によって公差が緩くなる場合があります。
- 材料の厚さと硬度
- 工具の摩耗とストローク速度
- 特徴の位置(平面と成形面)
4. 金属プレス加工で複雑な 3D 形状を実現できますか?
はい。順送金型と複合工具を使用することで、曲げ、オフセット、ルーバー、浅絞りなどの複雑な形状を実現できます。より深い形状の場合は、 深絞りスタンピング 壁が厚くなり、先細りになるという欠点はあるものの、採用されています。
5. 材料のスプリングバックは曲げ精度にどのような影響を及ぼしますか?
スプリングバックは、硬い材料やきつい曲げの場合に顕著になります。これを補正するには:
- 角度を少し曲げすぎる
- 材料の木目方向と焼き入れを考慮する
- スプリングバック効果に対抗するように設計された成形ツールを使用する
6. スタンプ部品の穴の間に必要な最小間隔はどれくらいですか?
歪みを避けるために、穴の間隔は少なくとも 材料の厚さの1.5倍 曲がった穴の近くの穴の場合は、 曲げ半径から離れた部分の材料厚さの2倍.
7. スタンプされた部品が完全に平らでないのはなぜですか?
平坦性の問題は次のような原因で発生する可能性があります:
- コイルセットとクロスボウの原板
- ピアス穴付近の材料の過剰な薄化
- 支持されていないエッジ付近の成形操作
ツールの調整や二次的な平坦化操作によって、この問題を軽減することができます。
8金属打ち抜き部品は、外観グレードにできますか?
はい、可能ですが、外観品質の要件は図面に明確に定義する必要があります。ツール設計、取り扱い方法、後処理(タンブリングや保護包装など)はすべて、外観品質基準を満たすように調整可能です。
9. 深絞り成形とストレッチ成形の違いは何ですか?
- 深絞り 材料を空洞内に引き込み、壁を厚くして底を閉じます。
- ストレッチ成形 シートをダイの上に伸ばし、壁を薄くし、通常は底が開いた状態になります。
深絞りは、強度が高く、密閉容器のような形状に最適です。
10. 金属プレス設計でコストを削減するにはどうすればよいでしょうか?
- 標準ゲージと一般的な合金を使用します。
- 必要な場合を除き、過度に厳しい許容範囲は避けてください。
- 製造可能性を考慮した設計特徴(例:間隔、半径、脚の長さ)
- 設計段階の早い段階でスタンピングハウスに相談してください。
参考文献
https://www.researchgate.net/figure/Schematic-presentation-of-the-conventional-deep-drawing-process_fig1_283671332
https://www.thefabricator.com/thefabricator/article/bending/r-d-update-edge-fracture-in-hole-extrusion-and-flanging-part-i
https://aminds.com/understanding-sheet-metal-stamping-guideline-for-buyers/