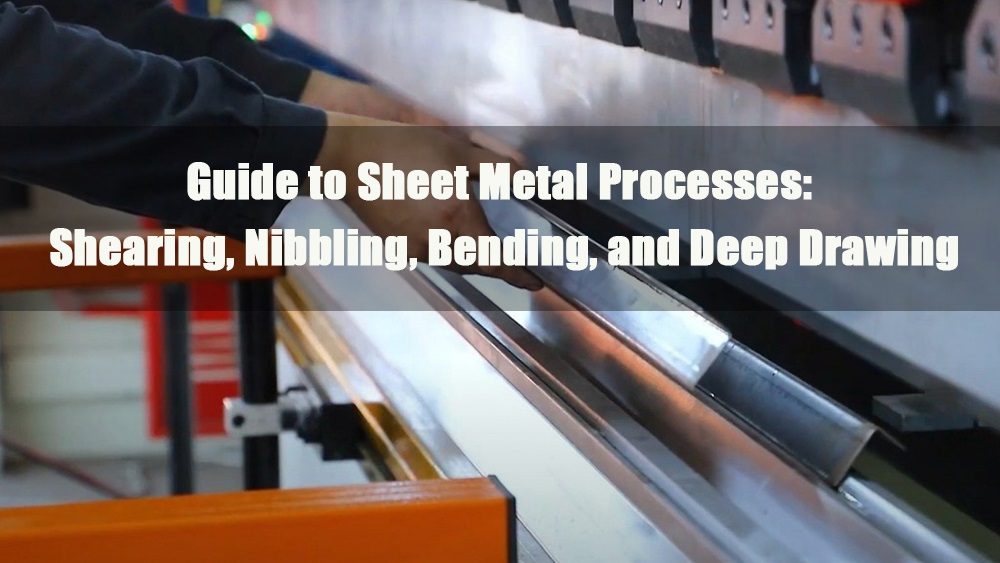
板金加工は現代の製造業の基盤であり、自動車、航空宇宙、建設、家電業界で広く利用されています。せん断、ニブリング、曲げ、絞り、エンボス加工、コイニングといったコアプロセスを理解することは、生産効率と製品品質の最適化を目指すエンジニアや製造業者にとって不可欠です。
1.0金属成形加工とは何ですか?
金属成形工程では、材料を一切削ることなく成形するため、材料の無駄がありません。板金は弾性限界を超える応力を受けますが、極限強度以下に抑えられるため、新たな永久的な形状が得られます。
一般的な金属成形操作には次のようなものがあります。
- 曲げ
- 描画
- エンボス加工
- 形にする
- コイニング(スクイージングとも呼ばれる)
2.0せん断とは何ですか?
せん断加工は、金属板、ストリップ、または棒材を直線状に切断する工程です。主に以下の3つの段階から構成されます。
- 塑性変形
- 破壊(亀裂の伝播)
- せん断(材料分離)
せん断機の上下の刃の間に金属ワークピースを置き、圧力をかけると、まず材料は塑性変形を起こします。圧力が増加すると、刃の刃先に亀裂が生じ始めます。そして、これらの亀裂が伝播して接触し、材料のせん断を引き起こします。
せん断機手動から油圧、機械式までさまざまなモデルが、特に大量生産や産業用途において、このプロセスを効率的かつ正確に実行するために使用されます。
3.0ニブリングとは何ですか?
ニブリングは、通常、ブランキングの代替として使用されます。板金から平らな部品を切り出すために設計されており、単純な輪郭から複雑な輪郭まで、さまざまな形状に適しています。この工程は主に少量の部品を生産する際に使用されます。
4.0曲げとは何ですか?
曲げ加工とは、直線状の金属板を曲面状に加工する加工方法です。曲げ加工では、材料は引張応力と圧縮応力の両方を受け、弾性限界を超えながらも極限強度以下の塑性変形が生じます。
一般的な曲げの種類は次のとおりです。
- U字曲げ
U曲げ(チャンネル曲げとも呼ばれる)は、U字型の金型キャビティを使用し、U字型のプロファイルを持つ部品を作ります。この操作は通常、 プレスブレーキ 機械 U字型のダイスを装備。 - V曲げ
V曲げ加工は、くさび形のパンチとVダイを用いて行います。Vの角度は鋭角から鈍角まで様々で、90°まで可能です。その汎用性と精度の高さから、プレスブレーキ加工において最も広く使用されている曲げ加工法の一つです。 - 角度曲げ
アングル曲げとは、板金を鋭角に曲げる一般的な用語です。また、 プレスブレーキ形状と必要な角度に応じて異なります。 - カーリング
カーリングとは、金属板の端面を型枠に沿ってカールさせる加工方法です。パンチとダイには、材料を成形するための部分的なキャビティが設けられています。加工後、パンチは引き込まれ、プランジャーによって成形品が排出されます。この加工方法は、ドラム缶、フライパン、鍋などの製造に用いられます。 - ロール曲げ
ロール曲げ加工は、複数のロールを用いて大型の板金部品を段階的に曲げ加工し、曲面状に仕上げる加工方法です。大型貯蔵タンク、圧力容器、配管、構造部品などの製造に広く用いられます。 - 4スライドマシンでの曲げ
この方法は比較的短い部品に使用されます。これらの機械は設計が様々で、金型の垂直方向と横方向の動きを利用して複雑な形状を成形します。 - エッジ曲げ
エッジ曲げにはカンチレバー荷重が含まれ、圧力パッドがワークピースをダイに押し当て、パンチが金属をエッジ上で曲げます。 プレス ブレーキ ワイピングダイを装備した機械でも、このタイプの曲げ加工が可能です。エッジ曲げは通常90°以下の角度に制限されますが、ワイピングダイはより大きな角度に対応できるように設計することも可能です。
圧力パッドとワイピングダイの複雑さにより、この方法はコストがかかりますが、大量生産に適しています。
5.0描くとはどういうことか?
絞り加工とは、平らな金属板をパンチで金型のキャビティに押し込み、材料を塑性流動させてカップ状の形状にする加工方法です。平らな板から中空部品を作成するために使用されます。
6.0エンボス加工とは何ですか?
エンボス加工は、装飾または機能的な目的で、板金に隆起または凹状のデザインを施すために使用されます。ロゴ、商標、部品番号、その他の識別マークを刻印するのに使用できます。
7.0形成とは何ですか?
成形では、金属に降伏点を超える応力を加えることで、パンチとダイの輪郭をそのまま再現し、新たな形状を永続的に保持します。絞り加工とは異なり、大きな金属流動は発生しません。この工程は、ドアパネル、スチール製家具、航空機の機体などの製造に用いられます。
8.0コイニング(スクイージング)とは何ですか?
コイニングとは、金属ブランクをパンチとダイの間に挟み、高圧をかける精密成形プロセスです。金属は冷間状態で塑性流動し、ダイキャビティを完全に充填します。このプロセスは、精緻な表面仕上げが施されたコイン、メダル、装飾部品の製造に用いられます。
9.0曲げの仕組みと一般的な方法を理解する
板金曲げ加工では、金属を直線軸を中心に曲げます。曲げ加工の内側の材料は圧縮され、外側の材料は引き伸ばされます。金属は塑性変形するため、応力が除去された後も曲げ加工部の形状が維持されます。通常、曲げ加工によって材料の厚さは大きく変化しません。
一般的な曲げ方法は次の 2 つです。
- V曲げV字型のパンチとダイを用いて行うこの方法では、鋭角から鈍角まで、幅広い曲げ角度に対応できます。一般的に少量生産の用途に使用され、プレスブレーキで行われることが多いです。V字型ダイは比較的シンプルで安価です。
- エッジ曲げこの方法では、加圧パッドでワークの底部を保持し、パンチでシートをダイのエッジ上で曲げます。複雑なワイピングダイを使用しない限り、エッジ曲げの角度は90°以下に制限されます。ワイピングダイはVダイよりも高価ですが、大量生産に適しています。
10.0曲げ加工における重要な要素:曲げ代、スプリングバック、力
曲げ許容値
曲げ半径が材料の厚さに比べて小さい場合、曲げ加工中に材料が伸びる傾向があります。この伸びを正確に予測することは、最終部品が設計仕様を満たすために不可欠です。曲げ代(BA)は、曲げ加工前の中立軸の推定長さであり、材料の伸びを考慮した値です。これは以下の一般式で計算できます。
BA = (π / 180) × A × (R + K × t)
どこ:
- BA = 曲げ許容値(mm)
- A = 曲げ角度(度)
- R = 内側曲げ半径(mm)
- t = 板厚(mm)
- K = 中立軸の位置を推定する係数(材料と曲げ条件に応じて、通常は0.33~0.5の間)
伸びは通常、曲げ半径がシートの厚さに比べて小さい場合に発生します。
スプリングバック
曲げ圧力が解放されると、材料に蓄えられた弾性エネルギーによって、元の形状に向かって部分的に回復します。これをスプリングバックと呼びます。スプリングバックとは、荷重除去後の工具角度に対する曲げ部品の開先角度の増加量として定義されます。
SB = θ₁ – θ₂
どこ:
- SB = スプリングバック(度)
- θ₁ = 曲げ後の板金部品の内角
- θ₂ = 成形工具の内角
曲げ力
曲げに必要な力は、パンチとダイの形状、材料の強度、板厚、部品幅などの要因によって異なります。最大曲げ力は、以下の式で推定できます。
F = (Kbf × TS × ω × t²) / D
どこ:
- F = 曲げ力 (N)
- TS = 材料の引張強度(MPa)
- ω = 部品の幅(mm)
- t = 板厚(mm)
- D = ダイ開口部寸法(mm)
- Kbf = 曲げ力係数
- V曲げの場合は33
- エッジ曲げ用33
11.0絞り加工:平らな板金から中空形状を製作する
絞り加工は、カップ型、箱型、その他の中空部品を作成するための板金成形プロセスです。平らな板金ブランクをダイキャビティに置き、パンチで押し込みます。ブランクホルダーは、加工中に材料を所定の位置に保持します。
代表的な用途は次のとおりです:
- 飲料缶
- 弾薬
- シンクと調理器具
- 自動車パネル
深絞りのメカニズムと段階
基本的なカップ描画プロセスでは、
直径 Dp のパンチを使用して、直径 Db のブランクを引き抜きます。
パンチとダイには、破れを防ぐためにコーナー半径 (Rp と Rd) が付いています。
パンチとダイの間にはクリアランスCが設けられています。
C ≈ 1.1 × t
2 つの力が適用されます。
変形のためのパンチ力(F)
金属の流れを制御するブランクホルダー力(Fh)
深絞り加工の段階は次のとおりです。
最初の接触 – 金属はダイとパンチの半径に沿って曲げられます。
矯正 – 以前に曲げられた部分は、ダイに引き込まれるとまっすぐになります。
引抜きと圧縮 – 材料がフランジからダイキャビティに流れ込みます。
摩擦(静的→動的)は流れに抵抗します。
フランジでの圧縮により厚みが増し、しわが発生する可能性があります。
引き抜き継続 – パンチは下方へと進み、金属を金型に引き込みます。
シリンダー壁に薄肉化が生じる場合があります。
ブランクホルダーの力と摩擦のバランスが重要です。
通常は潤滑が必要です。
描画におけるよくある欠陥
- フランジのしわ: 圧縮座屈による放射状の隆起。
- 壁のしわ: 垂直の壁に引き込まれたフランジのしわ。
- 引き裂き: 高い引張応力により、ベース付近に亀裂が開きます。
- 耳形成: シートの異方性により生じる不均一なエッジ (耳)。
- 表面の傷: 金型の表面が粗い、または潤滑が不十分なために発生します。
ストレッチフォーミング工程:航空宇宙および自動車向け大型輪郭シート
ストレッチ成形では、金属をフォームブロック上で弾性限界を超えて伸ばすことで、正確に輪郭が描かれた大型のシートを作成します。
スプリングバックは、以下の要因によって影響を受ける重要な問題です。
- 材質
- 厚さ
- 硬度
- 曲げ半径(半径が大きいほど、スプリングバックが大きくなります)
スプリングバックを低減する方法
V型フォームブロックを使用したオーバーストレッチ
コーナーセッティング:残留弾性応力を解放するためにコーナーをコイニングする
ストレッチ成形法
フォームブロック方式
ブランクは単一のフォームブロック(雄型)上に伸ばされます。
嵌合ダイ法
オスとメスの両方のダイを使用することで、より高い精度と再現性を実現します。
12.0結論
要約すると、せん断、ニブリング、曲げ、絞り、エンボス加工、コイニングなどの板金加工は、金属板を機能的で精密な部品に成形する上でそれぞれ重要な役割を果たします。
曲げ代、スプリングバック、金型設計など、これらのプロセスに影響を与えるメカニズムと変数を徹底的に理解することで、メーカーは欠陥を最小限に抑え、生産を最適化することができます。単純な平面部品を製造する場合でも、複雑な部品を製造する場合でも、
輪郭付きパネルの場合、これらの技術を習得することが板金加工を成功させる鍵となります。
13.0よくある質問
Q1: 板金加工における曲げと絞りの主な違いは何ですか?
A1: 曲げ加工は、大きな材料の流れを伴わずに軸を中心に金属を塑性変形させることで形状を変えますが、絞り加工は、金型の空洞に材料を引き込み、塑性流動を引き起こして中空の形状を形成します。
Q2: 曲げ加工時のスプリングバックを最小限に抑えるにはどうすればよいでしょうか?
A2: スプリングバックは、過剰に曲げたり、適切なツールを選択したり、弾性の低い材料を使用したり、設計時に適切な曲げ許容計算を適用したりすることで軽減できます。
Q3: ブランキングよりもニブリングが優先されるのはどのような場合ですか?
A3: ニブリングは、ブランキングダイがコストがかかったり実用的でない複雑な輪郭や少量生産の切断に適しています。
Q4: 深絞り加工時にしわが発生する原因は何ですか。また、しわを防ぐにはどうすればよいですか。
A4: しわはフランジ部の圧縮応力によって発生します。ブランクホルダー力、潤滑、工具形状を最適化することで、しわを最小限に抑えることができます。
Q5: 成形および絞り加工において潤滑が重要なのはなぜですか?
A5: 潤滑により、板金と工具間の摩擦が軽減され、表面の損傷、工具の過度の摩耗、破れやしわなどの欠陥が防止されます。