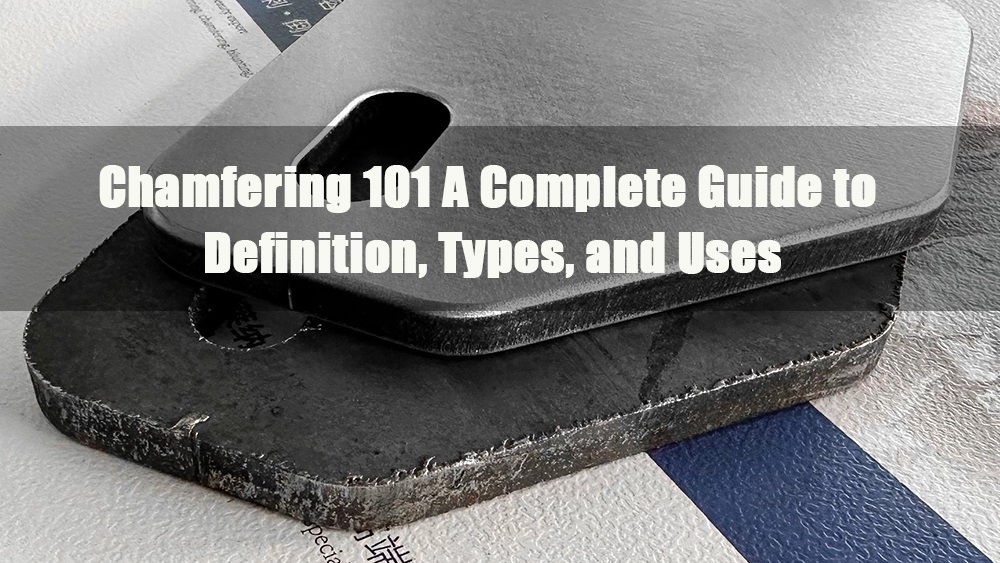
1.0面取りとは何ですか?
面取りは、部品のエッジから鋭い角を取り除くために機械加工や製造工程でよく用いられるエッジ処理です。機能性の向上、安全性の向上、そして部品の外観の向上にも貢献します。
面取りとは、特定の角度に設定された平面のことで、通常、隣接する2つの面の間の鋭角な90度の角を置き換えるために使用されます。丸みを帯びた遷移であるフィレットとは異なり、面取りは直線状のベベルを作成します。最も一般的に使用される面取り角度は45°ですが、設計や機能要件に応じて、30°、60°、またはその他のカスタム角度が適用される場合があります。
面取りは、金属、プラスチック、その他の素材で作られた部品に広く用いられています。例えば、ノートパソコンやスマートフォンの筐体のエッジは、滑らかな触り心地を実現し、取り扱い時の不快感を軽減するために、面取りやプレス加工が施されることがよくあります。
2.0面取りの種類
面取りは、形状と用途によって次の一般的なタイプに分類できます。
- 標準面取り(45°等間隔):
これは最も一般的な面取り方法で、隣接する2つの面に沿って、通常は45°の角度で均等に切削することで作成されます。対称性、加工性、再現性に優れているため、ブロック、ブラケット、平面部品に最適です。また、ほとんどのCADシステムではデフォルトの面取りオプションとして選択されています。 - 距離と角度による面取り(カスタム角度):
このタイプは、直線オフセットとカスタム角度(例:30°、60°)を指定して定義されます。傾斜精度や嵌合部品との位置合わせが求められる場合に使用されます。ガイド挿入やクリアランス管理が必要なアセンブリでよく使用されます。 - 非対称面取り(2距離面取り):
この場合、隣接する2つの面の面取りの長さが等しくなく、不等角度を形成します。片側のスペースが限られている場合や、組み立て時に特定の方向に力を加える必要がある場合に適しています。非対称の機械設計でよく使用されます。 - 穴エッジ面取り(リードイン面取り):
ドリル穴または機械加工穴の入口付近に塗布することで、ねじやボルトの挿入を容易にし、エッジの損傷を軽減し、ねじ山を保護します。通常、「C1.0 × 45°」と表記されます。ねじ穴、位置決め部、皿穴設計などでよく使用されます。 - 端面面取り:
シャフト、チューブ、またはディスクの端面には、ベベルエッジが施されます。外観を向上させ、鋭利なエッジを軽減し、アライメントを容易にします。回転部品では、エッジの摩耗を軽減する効果もあり、応力集中を緩和するためにフィレットと併用されることがよくあります。 - カスタム面取りプロファイル:
航空宇宙、医療機器、工具などの高精度または高仕様の用途に使用されます。これらには、可変角度、曲線遷移、複合面が含まれる場合があります。通常、多軸CNC加工、精密研削、または高度な3Dモデリングが必要であり、定義はCADで処理されます。
3.0面取りはどのように行いますか?
面取りは、部品の形状、必要な精度、生産設備に応じて、さまざまな加工方法で実現できます。一般的な加工方法としては、旋削、フライス加工、穴あけ、研削などがあります。
旋削面取り:
円筒形の部品に最も適しており、通常は旋盤で加工します。切削工具を回転するワークピースに送り込み、斜めのエッジを作成します。
一般的なツール:
- 45°ストレート工具:C型(直線)面取りに使用
- 半径ツール: R型(丸み)の面取りに使用します
この方法は、シャフトや類似部品の大量生産や精密面取りに最適です。
フライス面取り:
回転工具が固定されたワークピースの面取りを切削する、平らな表面または外側の輪郭に使用されます。
一般的なツール:
- 面取りフライスカッター:C型面取りに使用
- コーナーラウンディングエンドミル:R型面取りに使用
フライス加工は柔軟性が高く、複雑な部品の局所的な面取りに適しています。
ドリル面取り:
より大きな直径のドリルビットを用いてテーパー状のエッジを形成することで、穴の入り口部分に適用します。この方法は、個々の穴に対して迅速かつ効果的に使用できます。
注:この方法は効率的ですが、エッジに二次バリが発生する可能性があります。穴をきれいに仕上げるために、ボールエンドミルや専用のバリ取り工具を使用することが多いです。
研削と手作業による面取り:
バリ取りや、不規則な部分や繊細な部分の小さな面取りに使用します。
一般的なツール:
- ディスクグラインダー
- ハンドファイル
通常、ライン面取りや一般的なエッジの平滑化に使用されます。高精度な用途には推奨されません。生産における一貫した品質を確保するには、手動バリ取りよりも自動バリ取りシステムの使用が推奨されます。
4.0面取り穴とは何ですか? また、どのように定義されますか?
面取り穴とは、入口エッジが特定の角度(通常は45°)で面取りされた穴を指します。この角度のついた面は、いくつかの機能的な目的を果たします。
組み立てガイド: ネジ、ボルト、ピン、ブッシングなどの部品のスムーズな挿入を可能にします。
エッジ保護: 穴の周りの摩耗、欠け、エッジの破損のリスクを軽減します。
バリ除去: ねじ穴の場合、面取りをすると、嵌合部品に干渉したりねじ山を損傷したりする可能性のあるバリを除去するのに役立ちます。
構造的完全性の向上: 穴周りの応力集中を最小限に抑え、長寿命化に貢献します。
技術図面における面取り表記:
穴の面取りは通常、次のいずれかの形式で指定されます。
C1.0 × 45°: 45°の角度で1.0 mmの面取り深さを示します。
2 × 45°: 45°の角度で2mmの面取り幅を示します。
面取り穴は、ねじ穴、ダボ穴、位置決め穴、皿穴などに広く使用されています。信頼性の高い組み立てと耐久性が重要となる精密工学においては、標準的な設計手法となっています。
5.0面取りと半径の違いは何ですか?
機械設計と製造においては、 面取りと半径(またはフィレット) どちらも部品の鋭利な角を取り除くために使用されます。その目的は、フィット感、安全性、構造的完全性、そして外観を向上させることです。しかし、形状、用途、製造方法は大きく異なります。
比較項目 | 面取り | 半径/フィレット |
幾何学 | 角度のついた表面(通常は直線) | 曲面(滑らかな遷移) |
標準的な角度/サイズ | 通常は 45° ですが、30°、60° などになることもあります。 | 半径で定義されます(例:R1.0、R3.0) |
応用分野 | エッジ、穴のエントリ、位置合わせ機能 | 外部輪郭、コーナー、エッジ接合部 |
設計目的 | 鋭利なエッジを取り除き、組み立てをガイドし、嵌合を簡素化し、ストレスを軽減します | 外観を改善し、コーナーを強化し、応力集中を軽減します |
加工方法 | フライス加工、旋削加工、穴あけ加工 | フライス加工、CNC加工、金型成形 |
CAD表記 | C1.0 × 45°(深さ × 角度) | R2.0(半径指定) |
注記:技術的には、 面取り は直線的な角度のカットを指し、 半径 または フィレ 丸みを帯びた遷移を示す。非公式な用法では、 ベベル は面取りと同じ意味で使用されることもありますが、設計図や CAD モデルでは明確に区別する必要があります。
6.0面取りが重要な理由
面取りは、高品質な部品や板金加工において不可欠な設計・製造プロセスです。安全性、組立効率、耐久性、接合性能の向上に重要な役割を果たします。主な利点は以下のとおりです。
- 安全性の向上:
機械加工された金属部品には、鋭利なエッジやバリが残っていることが多く、取り扱い、取り付け、使用中に切り傷や怪我の原因となる可能性があります。面取り加工により、これらの鋭利な角が除去され、怪我のリスクを軽減できます。特に、子供が扱う可能性のある製品では、保護を強化するために大きな面取りが必要となる場合があります。 - 簡素化された組み立て:
面取りは、ネジ、ピン、ファスナーなどの部品の導入部として機能します。部品を嵌合穴に導き、干渉を最小限に抑え、位置合わせの難しさを軽減することで、最終的には組み立てプロセスをスピードアップします。 - 応力集中の軽減:
鋭利な90度エッジは、荷重や振動によって応力が集中し、ひび割れや疲労破壊につながる可能性があります。面取りは、重要な接合部における応力を均等に分散させ、構造全体の信頼性を向上させます。 - 耐久性と機械的完全性の向上:
鋭利なエッジは、摩擦や衝撃により、時間の経過とともに欠け、ひび割れ、剥離が発生しやすくなります。面取りされたエッジは、エッジの移行をスムーズにし、損傷の可能性を低減するとともに、機械への破片の侵入を防ぎ、故障リスクを低減します。 - 最適化されたジョイントパフォーマンス:
面取りは、溶接、接着、ボルト接合において、より良好なエッジ状態を実現します。応力集中を最小限に抑え、シール面を改善し、接合部の完全性を強化します。 - 製造効率の向上:
大量生産においては、CNCプログラミングによって面取りを標準化・自動化できます。これにより、手作業による仕上げ工程が削減され、部品間の品質の一貫性が向上し、全体的な生産スループットが向上します。
7.0一般的な面取り工具の分類と適用ガイド
面取りは金属加工において一般的な仕上げ加工であり、鋭利なエッジの除去、組み立ての容易化、溶接品質の向上、部品の美観向上などに用いられます。加工方法、部品の形状、用途に応じて、面取り工具は主に4つのタイプに分類されます。
7.1面取り機
- ベンチトップ面取り機: 板金、フラットバー、パイプ – バッチ生産に高い安定性、角度と深さの調整が可能
- 手持ち面取り工具: 不規則なエッジ、現場での修理 – ポータブルで柔軟性があり、小ロットやさまざまな形状に最適
- パイプ面取り機: 鋼管およびステンレス鋼管 - パイプ端面用に設計されており、1回のパスで内側、外側、および表面の面取りが可能です。
- 両頭面取り機ロッドエンドとチューブエンド - 両端同時加工、高効率・高精度、自動化ラインに最適(例:サーボ駆動モデル)
7.2CNC面取り工具(旋盤/ミル/CNC用)
- 面取りインサートCNC旋盤 - ツールホルダーに取り付けられ、連続した繰り返しの面取りに適しています
- 面取りエンドミルCNC加工センター - 共通角度:30° / 45° / 60°;エッジや穴の面取りに最適
- センタードリル: 面取りによる穴の位置決め - パイロット穴と面取りを1つのステップで完了
- コンビネーション面取りツール: 内側と外側のエッジの統合 - 面取り、バリ取り、エッジの丸めなどの複合プロセスを1つの操作で効率的に実行
7.3手動・軽量面取り工具(修復・エッジ仕上げ用)
- バリ取りツール: 内穴、鋭いエッジ - 手動式、コンパクトで使いやすく、局所的な仕上げに適しています
- 手動面取りナイフ: エッジ、穴の入り口 - 迅速かつ簡単な操作。軟質金属や軽作業に最適
- ヤスリ / 研削ホイール / サンドペーパー: 多様なエッジ形状 – 低コストで柔軟なハンドリング。手作業によるエッジ仕上げや表面平滑化に便利
7.4レーザー/プラズマ/ウォータージェット切断用面取りアタッチメント
これらは、エッジ遷移とベベル準備のための自動化システムに統合されています。
- 角度制御モジュール付きレーザー切断ヘッド: 45°のベベルに適しています
- プラズマベベルカッティングヘッド: 切断中の高速面取り用に設計
- 多軸ウォータージェットチルトヘッド: 角度制御による正確なエッジ面取りが可能
7.5推奨アクセサリとツールの組み合わせ
アングルグラインダーユーザー向け: フラップディスクを強くお勧めします
内側のコーナーには湾曲したフラップディスク、平らなエッジには直線状のフラップディスク
非鉄金属の場合は、熱による変色や腐食を抑えるために、クーラント添加剤を含んだ研磨布を使用してください。
ダイグラインダー/エアグラインダーユーザー向け: 超硬バーを使用する
構造: タングステンカーバイドカッティングヘッド + 工具鋼シャンク
歯のプロファイル:
- Z6クロスカット: 高い材料除去率、迅速な処理に適しています
- Z3シングルカット: より滑らかな表面仕上げを実現
- 造船プロファイル: 重作業向けに最適化。約30%の高除去率
8.0ツール選択ガイド(アプリケーションシナリオ別)
アプリケーションのニーズ: 推奨ツールタイプ
- パイプ端の準備: パイプ面取り機, 両頭面取り機
- CNC加工部品:面取りエンドミル、面取りインサート
- 不規則なエッジ / 現場修理: 手持ち面取りツール、手動面取りナイフ
- 自動化された大量生産ライン:CNCツールシステム、サーボ駆動面取り機
- 溶接準備のためのベベル加工:レーザーまたはプラズマベベル切断システム
9.0CAD における面取りエッジとは何ですか?
CAD(コンピュータ支援設計)において、面取りとは、交差する2つの面の間に、元の鋭角なエッジを置き換えて角度のついた遷移面を作成することを指します。この設計要素は、現実世界の製造の詳細をシミュレートするだけでなく、次のような機能的な利点ももたらします。
- 組み立て性の向上: 面取りされたエッジは嵌合部品をガイドし、組み立ての精度と効率を向上させます。
- 強化された構造性能: 鋭角な角による応力集中を軽減し、部品全体の強度を高めます。
- 外観と製造性の向上: より明確なプロセス計画と下流工程のための加工フィーチャを表します。
ほとんどの主流の CAD ソフトウェア (AutoCAD、SolidWorks、Fusion 360 など) は、いくつかの面取り定義方法をサポートしています。
- 等間隔面取り: 隣接する面の両方に同じオフセットを適用します (一般に C タイプ面取りと呼ばれます)。
- 距離と角度の組み合わせ: 特定のエッジの長さと対応する角度を定義します。
- 非対称面取り: 隣接する面ごとに異なる距離を割り当てます。
面取りは通常、3D モデリングの初期段階で定義され、製造と検査を容易にするために 2D 技術図面で自動的に表現されます。
10.0CADで面取りを作成する方法
10.1方法1:等距離面取り(対称)
両方の隣接するエッジに同じ面取り距離を適用する場合に使用します。通常は標準の C タイプ面取りに使用されます。
手順:
- 選択してください 面取り 「変更」または「機能」メニューからツールを選択します。
- 面取りを適用するエッジまたはコーナーを選択します。
- 均一な距離(例:2 mm)を入力します。
- 面取りを確認して適用します。
10.2方法2:距離と角度の面取り
ピン挿入や穴のリードインなど、特定のガイド角度を必要とする機能に最適です。
手順:
- アクティブ化する 面取り
- ターゲットエッジを選択します。
- 直線距離(例:3 mm)と希望の角度(例:45°)を設定します。
- ソフトウェアによって角度の付いたサーフェスが自動的に作成されるので、適用を確認します。
10.3方法3:2距離面取り(非対称)
各面に異なる面取り長さを割り当てることにより、非対称アセンブリまたはスペースが制限された領域に使用されます。
手順:
- 起動する 面取り ツールを使用して、ターゲット エッジを選択します。
- 隣接する面に対して 2 つの異なる距離を設定します (例: サイド A: 5 mm、サイド B: 2 mm)。
- 非対称面取りを生成することを確認します。
11.0面取り vs. ブレークエッジ
ブレイクエッジ 安全性と取り扱いやすさを考慮して、鋭角部を除去するために施される、非常に小さな面取り(通常0.01mmから0.5mm)を指します。これは機能上重要ではない特徴とみなされ、技術図面では次のような注記とともに示されるのが一般的です。
「鋭い角はすべて壊してください。」
「バリや鋭角を取り除く」
特徴:
寸法精度は厳密には要求されない
通常は手作業または自動バリ取りで実行され、プロセスの慣例と見なされます
面取り対照的に、は寸法と角度が制御された、正確に定義されたデザイン特徴です。その機能はエッジの柔らかさを増すだけでなく、以下の機能も備えています。
- 組み立てガイド
- 応力集中の軽減
- 美観の向上
- 正確なフィットまたはアライメント
面取りは通常CADモデル内で指定され、技術図面に明確に注釈が付けられます(例: C1.0 × 45°)、意図的かつ制御された幾何学的要素として扱われます。
12.0面取りと皿穴
どちらも傾斜面を伴いますが、その機能と設計意図は大きく異なります。
カテゴリ | 面取り | 皿穴 |
関数 | エッジの破壊、組み立てガイド、位置合わせ、そして美観 | 取り付け面と面一の皿頭ネジ |
位置 | 任意のエッジ(内側または外側) | 穴の内側 |
幾何学 | シンプルな角度の顔 | 円錐形の凹部、通常は同心円状 |
共通角度 | 30°、45°、60°(カスタマイズ可能) | 82°、90°(標準化) |
典型的なコールアウト | C1.0 × 45° | 皿穴 Ø8 × 90° |
ネジの取り付け | 挿入を助けるかもしれないが、ネジに特有のものではない | 標準の皿頭ネジ仕様に適合 |
まとめ皿穴は標準化されており、ファスナー専用に作られていますが、面取りはより幅広い目的に使用され、設計の柔軟性が向上します。
13.0面取りとバリ取り
どちらのプロセスもエッジ品質を向上させますが、目的、方法、制御が異なります。
カテゴリ | 面取り | バリ取り |
意味 | 正確な寸法の角度カット | バリ除去によるエッジの洗練 |
コントロール | CADで定義され、厳密に寸法が付けられている | 多くの場合、サイズは指定されず、プロセス主導型 |
方法 | 旋削、フライス加工、CNC加工 | 研磨、ブラッシング、手作業によるヤスリ掛け、振動等。 |
目的 | 機能的または構造的な特徴 | 安全性と表面仕上げの改善 |
形状 | 固定角度と深さ | 不規則、丸み、または微細面取り |
まとめ面取りはデザイン重視で寸法管理が重要視される一方、バリ取りは安全性と表面の清浄性を重視します。機能や製造ニーズに応じて、これら2つは個別に、または組み合わせて適用できます。
14.0エンジニアリングにおける面取りとは何ですか?
工学では、 面取り 部品の鋭利なエッジを置き換えるために精密に機械加工された角度のある面です。特に指定がない限り、標準的な面取り角度は通常45°です。
面取りの主な機能:
- 鋭角の除去: 応力集中点を減らし、構造の完全性を高めます。
- 組み立て補助: ファスナーを穴にガイドしたり、組み立て時に部品の位置合わせを容易にします。
- 安全性の向上: 切り傷、衝撃による損傷、または取り扱いに関連する怪我のリスクを最小限に抑えます。
- インターフェースの最適化: 接触面を滑らかにすることで、溶接、接着接合、ボルト接合の品質を向上させます。
技術図面では、製造性と検査の一貫性を確保するために、面取りの寸法と公差は国際技術規格に従って記入する必要があります。一般的な規格には以下が含まれます。
- ASME Y14.5
- ISO 13715
これらの規格は、精密機械設計における再現性と信頼性を実現するために重要です。
参考文献
violintec.com/sheet-metal-and-stamped-parts/chamfers-vs-radii-in-sheet-metal-fabrication-know-the-difference/
https://en.wikipedia.org/wiki/Chamfer